In the automotive industry, gas detection is an essential technology for ensuring operator safety and reducing the environmental impact of manufacturing processes. Manufacturing plants and workshops are complex environments with numerous processes that can generate hazardous or harmful gas emissions. These include welding gases, solvent vapors, chemicals used in painting, and even emissions from chemical reactions in materials processing.
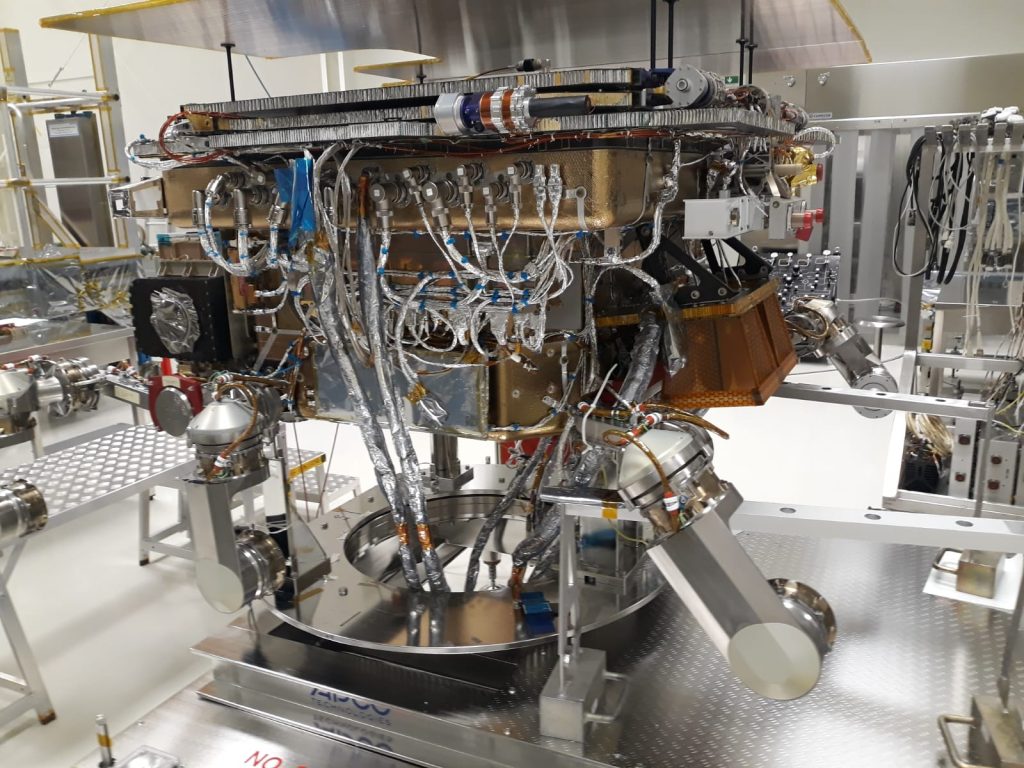
Automotive industry: the advantages of gas detection
Within the automotive industry, the adoption of gas detection systems helps companies monitor these environments in real time, enabling them to quickly identify hazardous situations and take corrective action to protect workers and the surrounding area. Key benefits include:
- Worker Safety: Operators at automotive manufacturing sites are often exposed to potentially harmful gases, such as carbon monoxide (CO), nitrogen oxides (NOâ‚“), and volatile organic compounds (VOCs) emitted during welding, painting, and assembly processes. Detecting these gases early is critical to avoid poisoning or explosions.
- Environmental Protection: Controlling industrial emissions helps minimize the environmental impact of automotive plants. Untreated harmful gases can in fact contribute to air pollution and climate change.
- Operational Efficiency and Regulatory Compliance: Meeting environmental and safety regulations is critical for automotive companies. Installing advanced gas sensors allows real-time monitoring of emissions and ensures that pollution levels are always within required limits, avoiding penalties and production downtime.

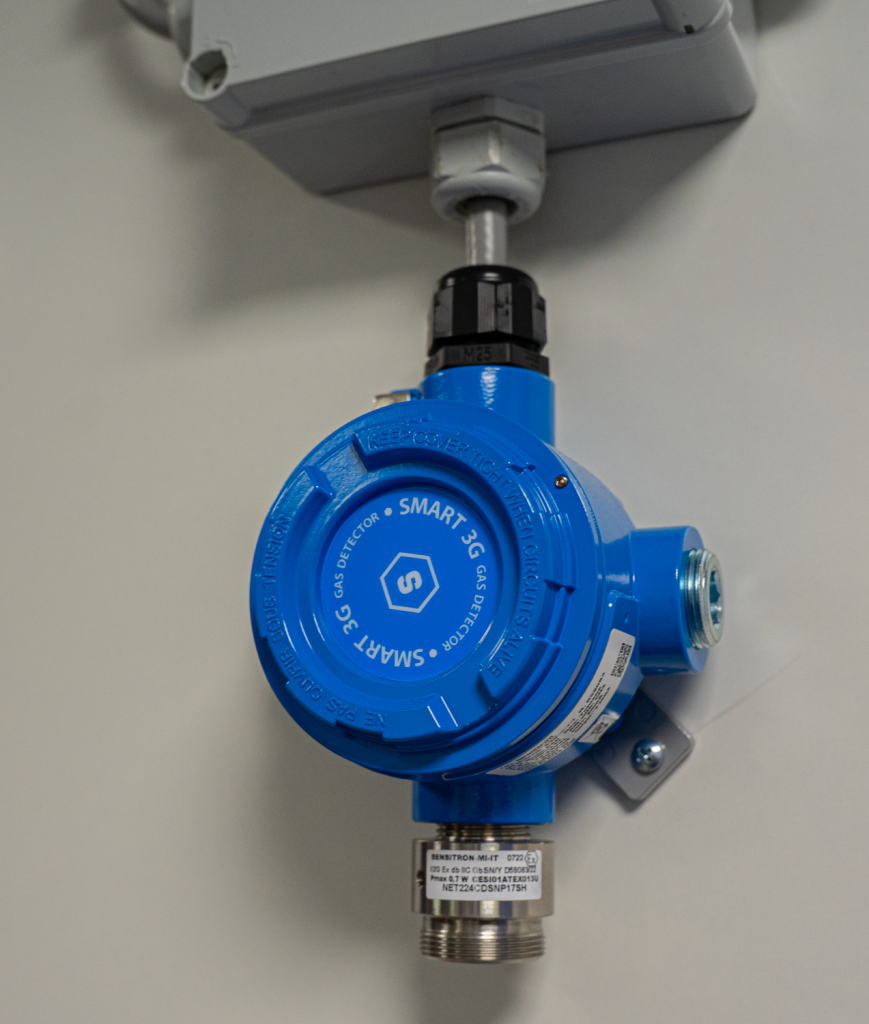
Technologies for gas detection in the automotive industry
Several types of sensors are used in the automotive industry, each designed to detect specific types of gases. Here are the most common ones:
- Catalytic Sensors: Used primarily to detect flammable gases, these sensors take advantage of gas combustion on a catalytic surface. They are common in environments where there is a risk of flammable vapors, such as in painting and surface treatment areas.
- Electrochemical Sensors: These sensors are ideal for detecting toxic gases such as carbon monoxide (CO) and sulfur dioxide (SOâ‚‚). They are used in areas with combustion processes or in enclosed spaces where hazardous gases could accumulate.
- Infrared (IR) Sensors: These sensors detect gases such as COâ‚‚ and hydrocarbons by measuring the absorption of infrared light. They are particularly effective in monitoring industrial emissions and keeping an eye on COâ‚‚ levels in processing areas.
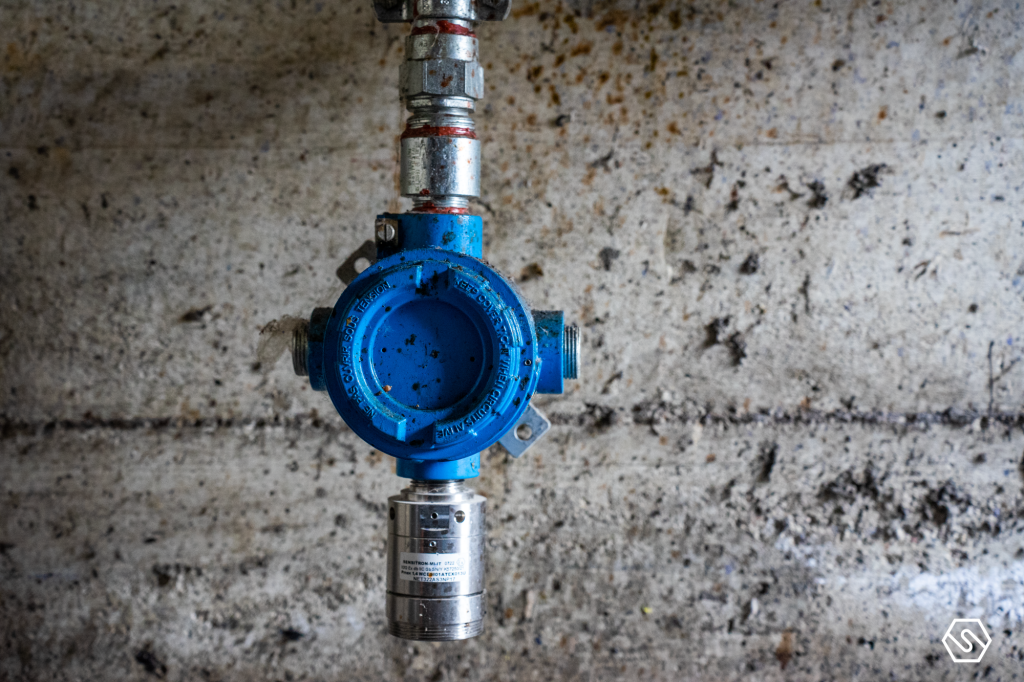
Automotive industry: the most common applications
Gas detection systems find application in several key areas within automotive manufacturing plants:
- Paint Areas: Solvents and chemicals that emit volatile organic compounds (VOCs) and other toxic gases are used here. By detecting these gases, concentration levels are kept within safe limits, protecting both workers and the environment.
- Welding and Assembly Areas: These processes generate gases such as carbon monoxide, nitrogen oxides and ozone, all of which are potentially harmful. Sensors placed in welding areas help maintain a safe environment for operators.
- Monitoring Emissions in Combustion Processes: In engine testing or vehicle test departments, it is crucial to monitor exhaust gases. Gas sensors are placed to monitor COâ‚‚, CO, and NOâ‚“ levels, ensuring that facilities comply with emission regulations.
- Flammable Material Storage Areas: In these areas, detection of hydrocarbon vapors and other flammable compounds is essential to prevent fires and explosions.
Discover our produtcs
Sensitron gas detectors are suitable for use in any application:
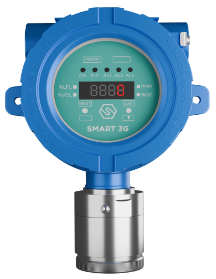
SMART 3G D2
Suitable for detecting the presence of flammable substances, toxic gases, refrigerants and oxygen in classified areas.ATEX, IECEx and SIL2/3 certified
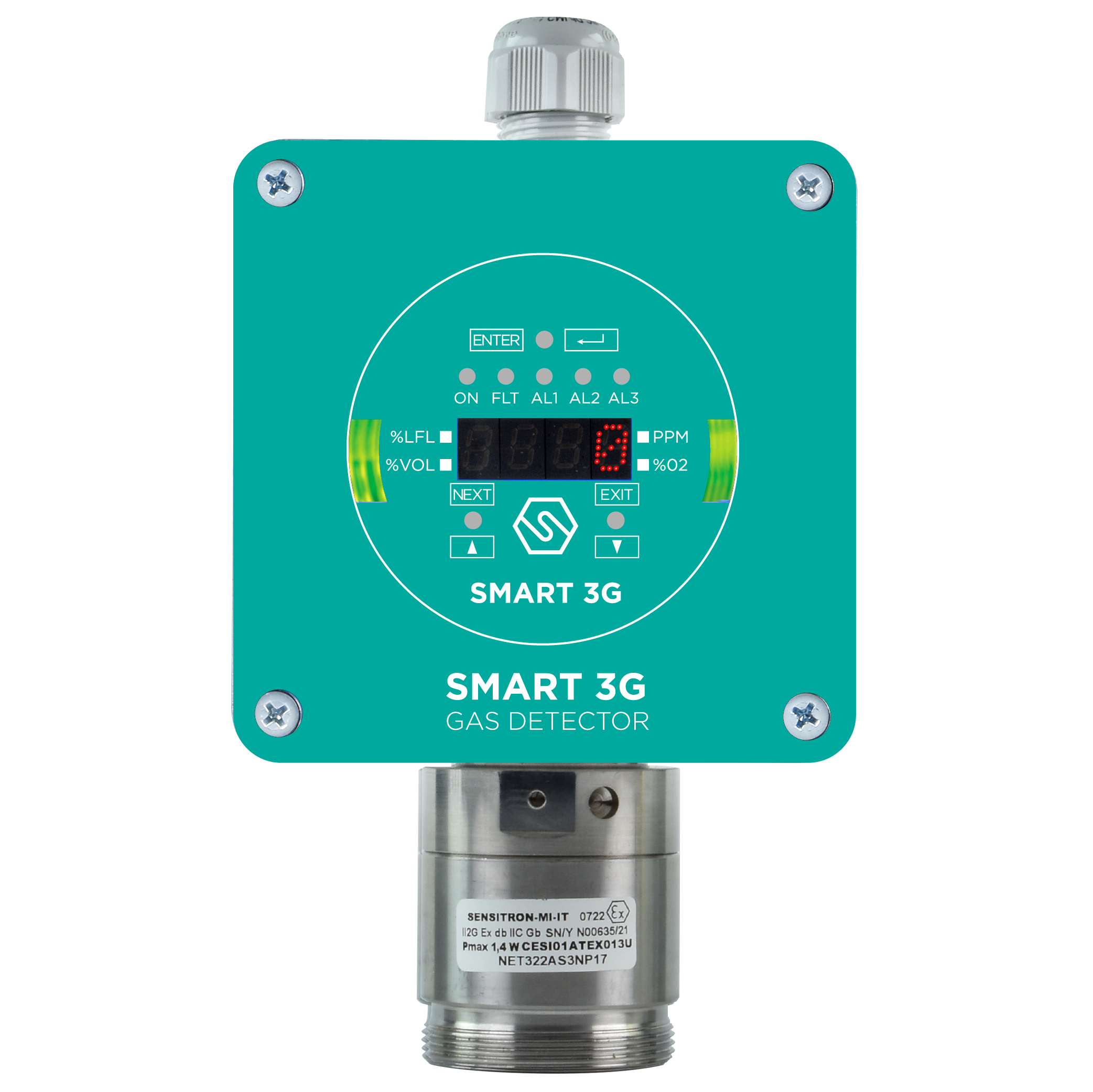
SMART 3G D3
Suitable for detecting in classified areas,ATEX, IECEx and SIL2/3 certified, enables non-intrusive field calibration.
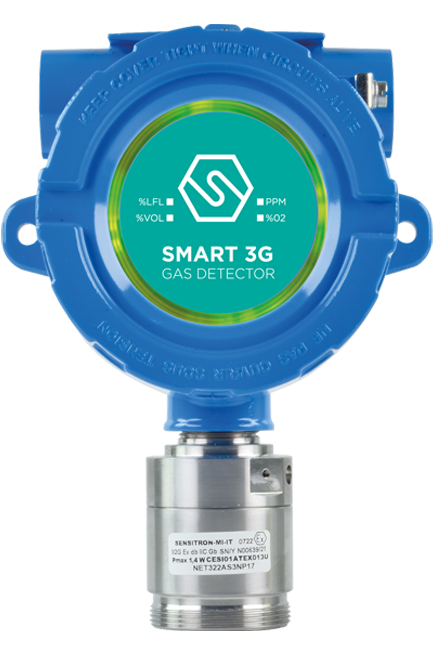
SMART 3G C2
Suitable for detecting, in classified areas, the presence of flammable substances (% LFL), toxic gases in ppm, refrigerant gases or for the detection of oxygen deficiency or excess.
Our certifications
Within hazardous environments where strict safety standards must be met, it is important to use products that are certified and in line with regulations. Learn about our certifications:
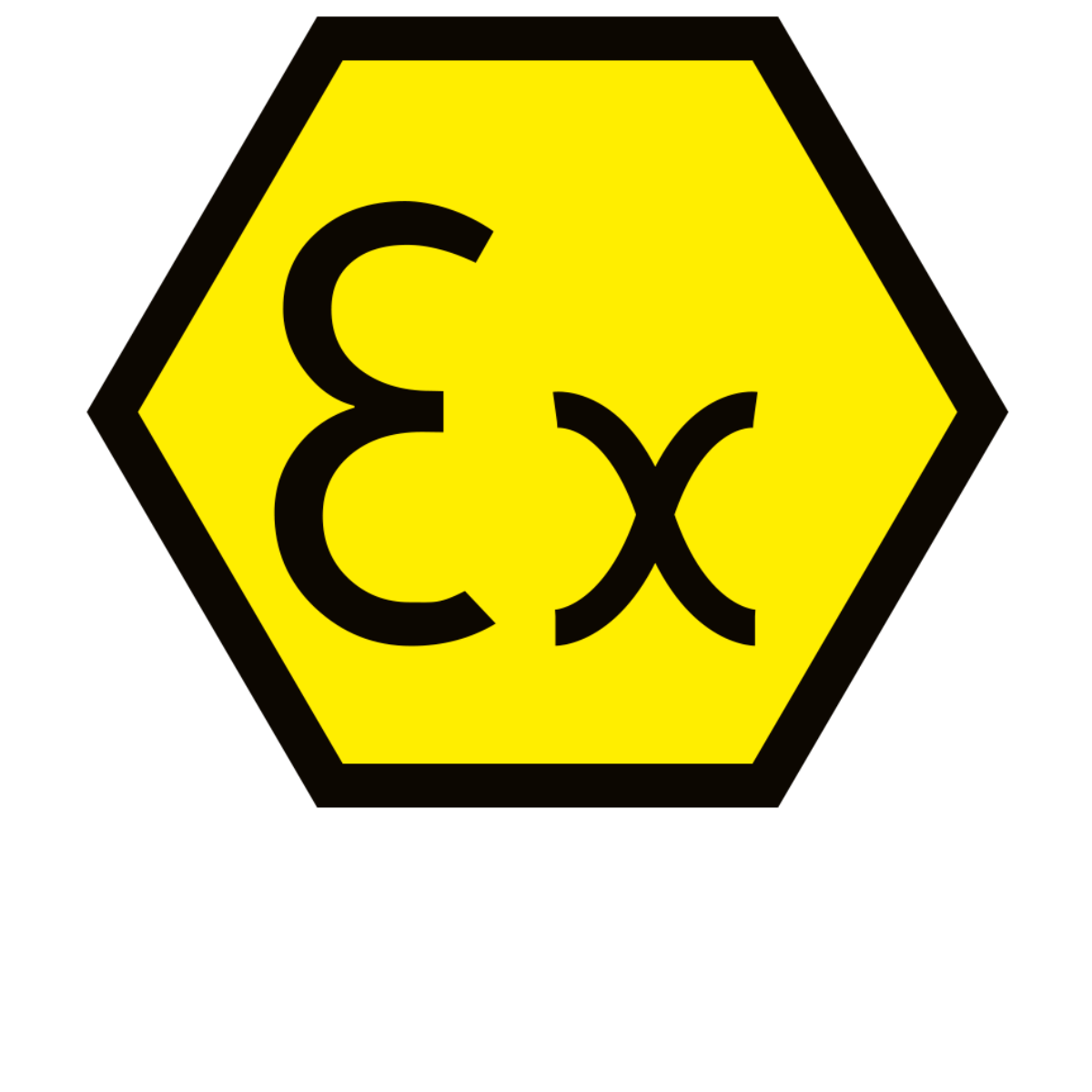
ATEX
The Directive sets out the requirements and assessment of equipment intended for use in potentially explosive atmospheres.
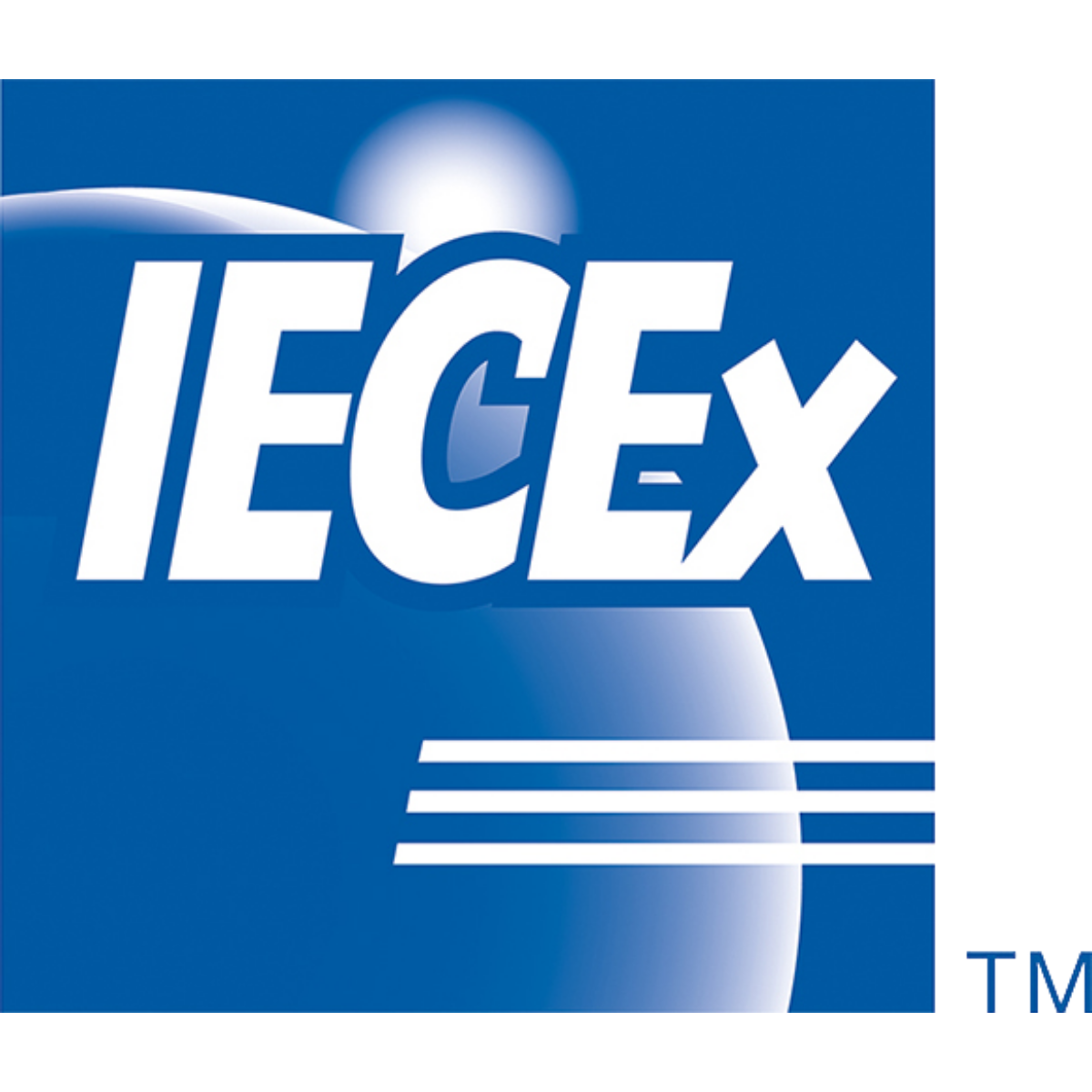
IECEx
The IECEx system is an international certification system. It is developed by the International Electrotechnical Commission.
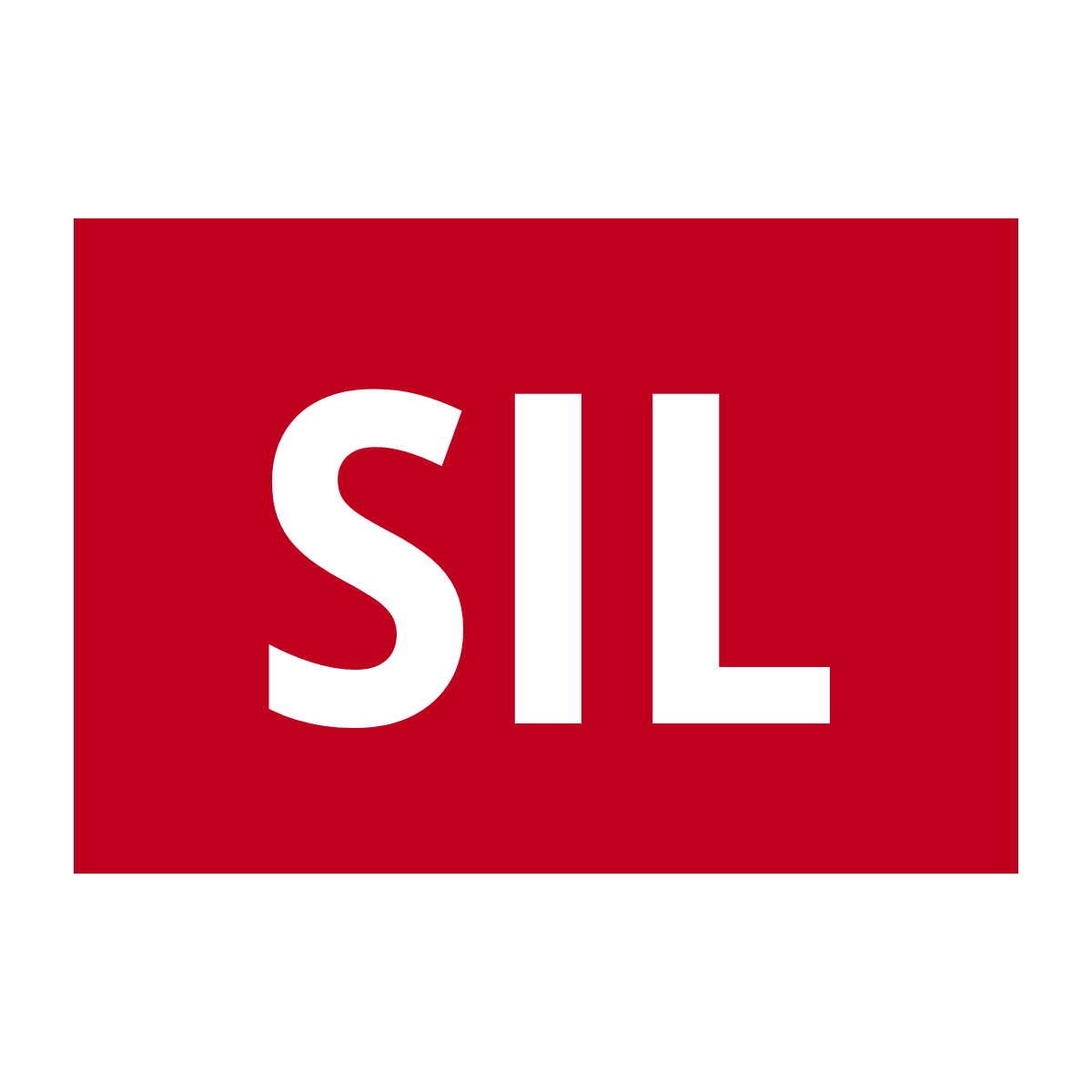
SIL
The Safety Integrity Level (SIL) is the ability to reduce the assessed risk by ensuring the reliability of safety systems.