In aerospace, the use of oxygen and hydrogen is crucial but carries high risks. These two elements, as useful as they are dangerous, require a rigorous approach in terms of safety, design and monitoring of the environments in which they are used. In this article, we take a closer look at the critical issues involved in handling oxygen and hydrogen in aerospace components and how Sensitron helps to ensure maximum protection of people and infrastructure.
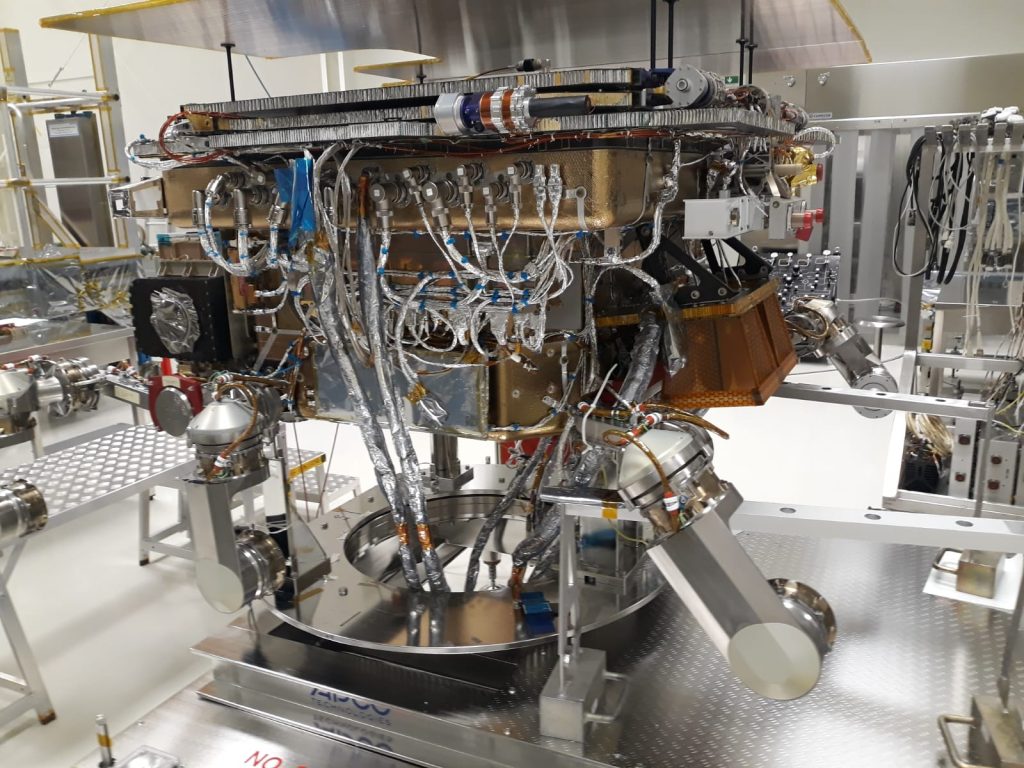
Aerospace industry: why are oxygen and hydrogen so widely used?
Oxygen and hydrogen are key elements in many aerospace applications, from propulsion to life support. However, their use requires careful handling to avoid significant risks:
Oxygen: Used for life support in space habitats, space suits and combustion propulsion systems. However, at high pressures or in confined environments, it can render materials highly flammable.
Hydrogen: This is a key propellant, particularly in liquid form in rockets (think of the famous LH2/LOX mix). Very light and with high energy density, it is however extremely volatile and permeable, with a very high risk of explosion in the event of an undetected leak.
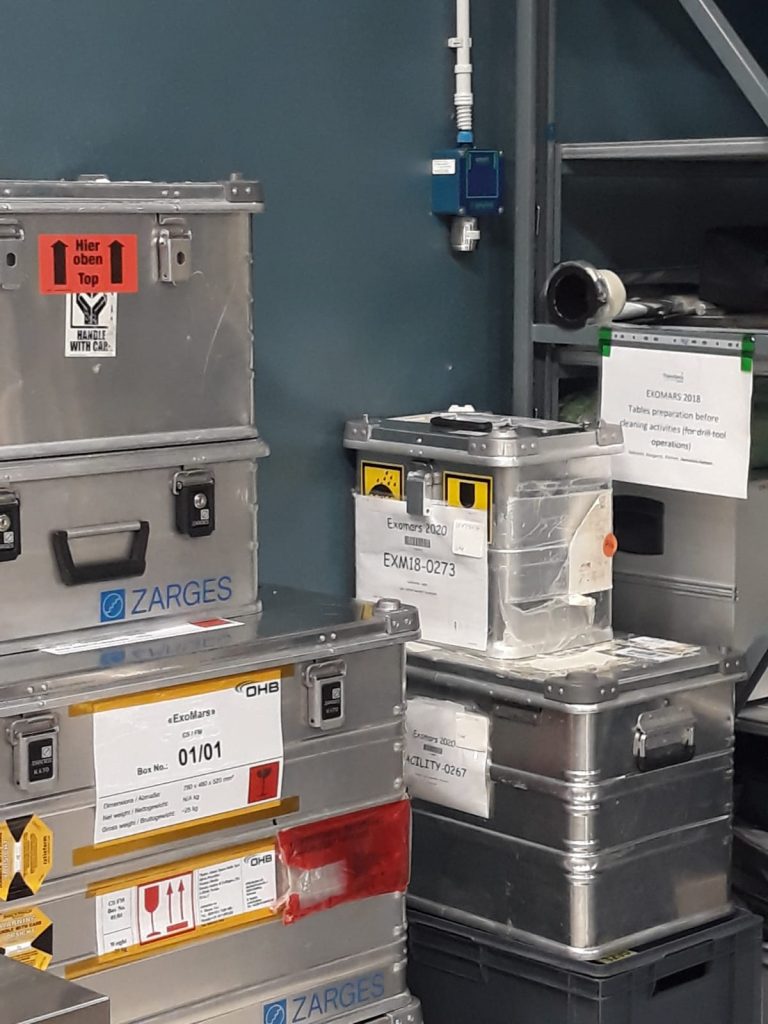
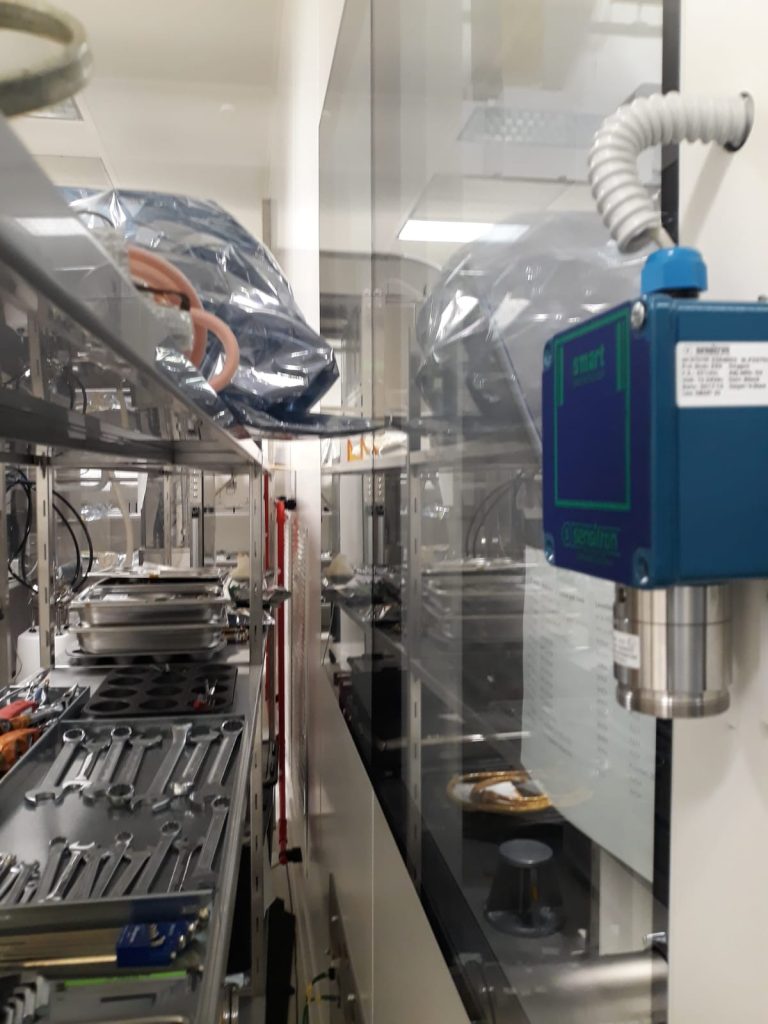
Main security challenges
The safe handling of oxygen and hydrogen involves complex technical challenges related to the nature of these gases. Let us take a look at the main critical aspects:
-
Permeability of Materials
Hydrogen can penetrate the molecular structure of many materials, causing brittleness (hydrogen embrittlement) and possible structural failure. -
Combustibility High
Both gases can create highly combustible environments even with small concentrations. A spark or local overheating is enough to trigger violent reactions. -
Continuous Monitoring
In environments such as cabins, cryogenic tanks or combustion chambers, it is essential to detect every minute leak to avoid catastrophic damage.
Oxygen and hydrogen detection technologies
To ensure safety in aerospace environments, it is essential to have detection technologies that are reliable, accurate and suitable for extreme operating conditions:
For hydrogen, the most commonly used technologies include:
-
Semiconductor sensors: react to the presence of gas by changing electrical conductivity; they are compact and sensitive, but can be affected by other interfering gases.
-
Electrochemical sensors: offer good selectivity and are ideal for detecting low concentrations.
For oxygen, the main technologies are:
-
Electrochemical sensors: very common for use in controlled or confined environments due to their accuracy and ease of integration.
The choice of technology depends on various factors: concentration range, required response time, operating environment, weight and compatibility with other systems. And it is in the intelligent integration of these technologies that the game of safety is played.
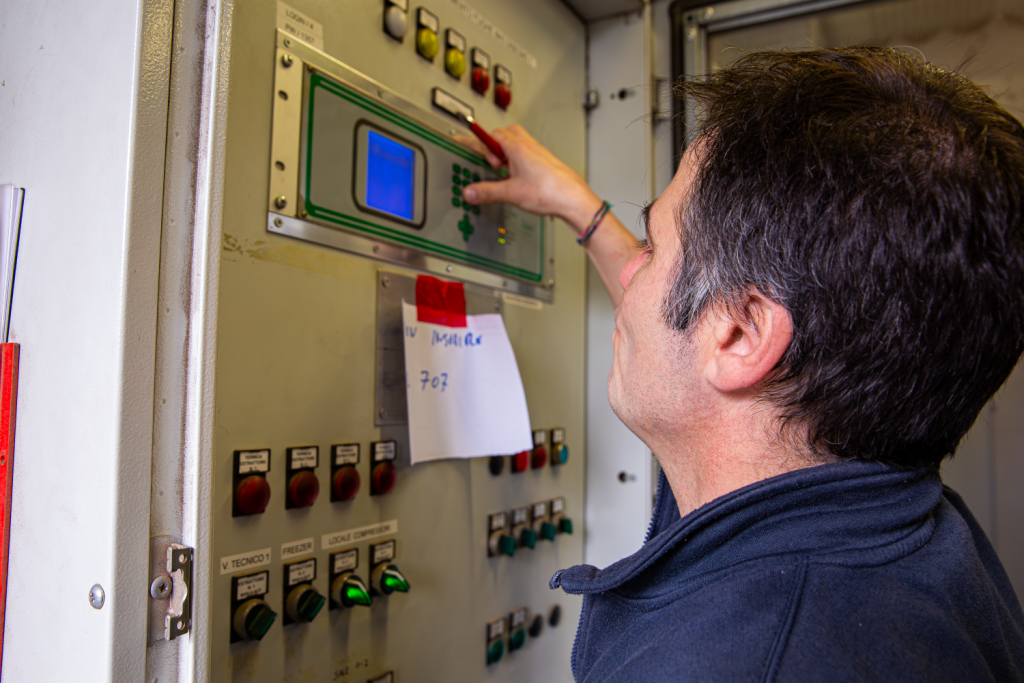
Aerospace industry: why choose Sensitron
To meet these challenges, it is essential to have reliable technologies designed to operate in extreme conditions.
Sensitron develops advanced gas detection solutions suitable for even the most extreme aerospace environments. Our sensors are designed to:
-
Withstand extreme conditions of temperature, pressure and vibration.
-
Detect minute concentrations of hydrogen and oxygen with extremely fast response times.
-
Integrate intelligent systems for alarms, automatic shut-downs and predictive diagnostics.
In addition, thanks to ATEX certification and other international approvals, our solutions find application not only in aerospace but also in critical infrastructure on the ground: laboratories, test centres, storage and maintenance facilities.
Discover our produtcs
Sensitron gas detectors are suitable for use in any application:
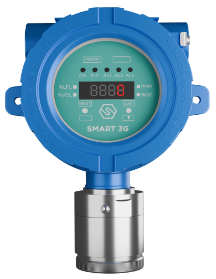
SMART 3G D2
Suitable for detecting flammable substances, toxic gases, refrigerants and oxygen in classified areas.ATEX, IECEx and SIL2/3 certified.
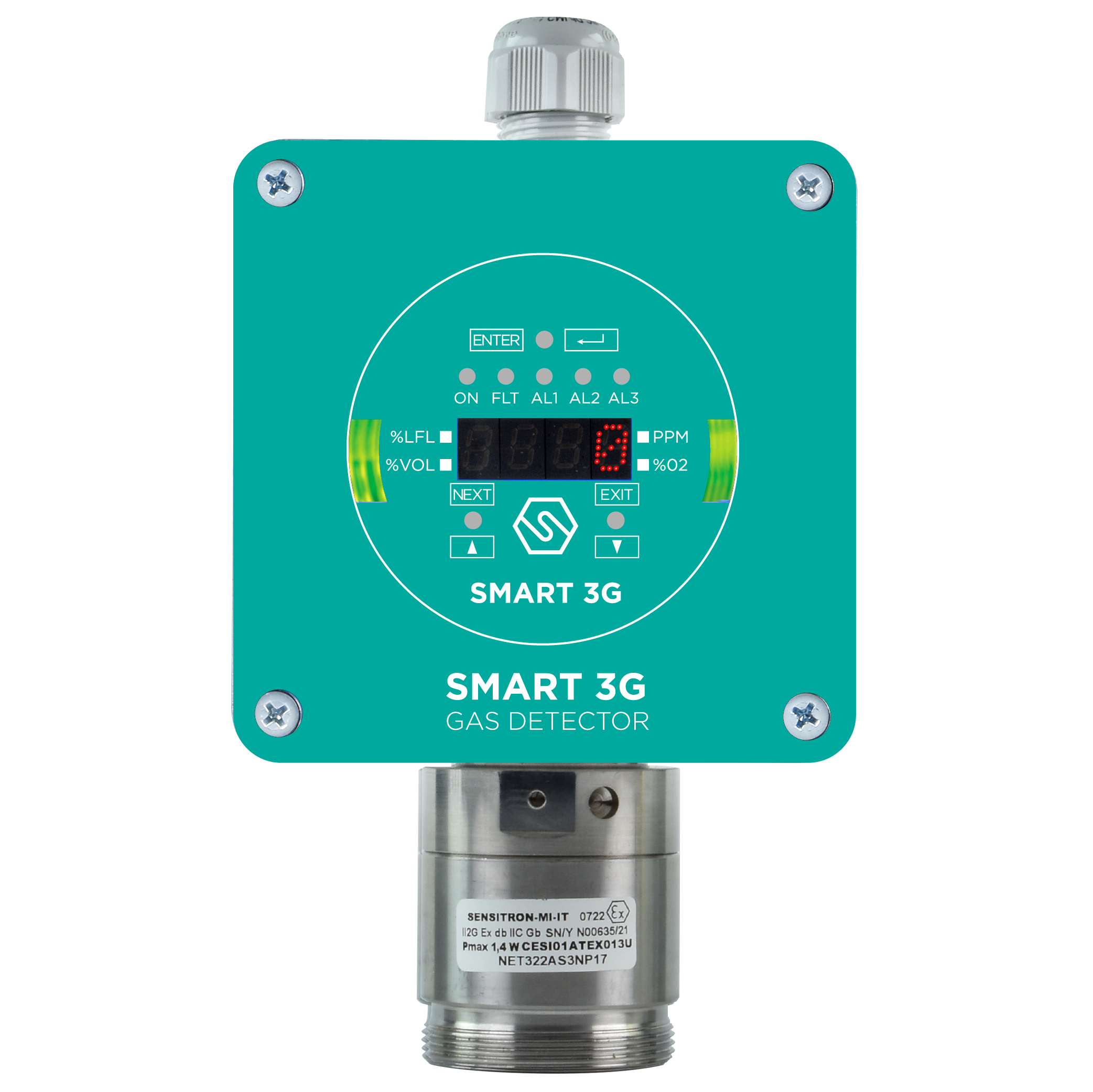
SMART 3G D3
Suitable for gas detection in classified areas, ATEX, IECEx and SIL2/3 certified, allows for non-intrusive field calibration.
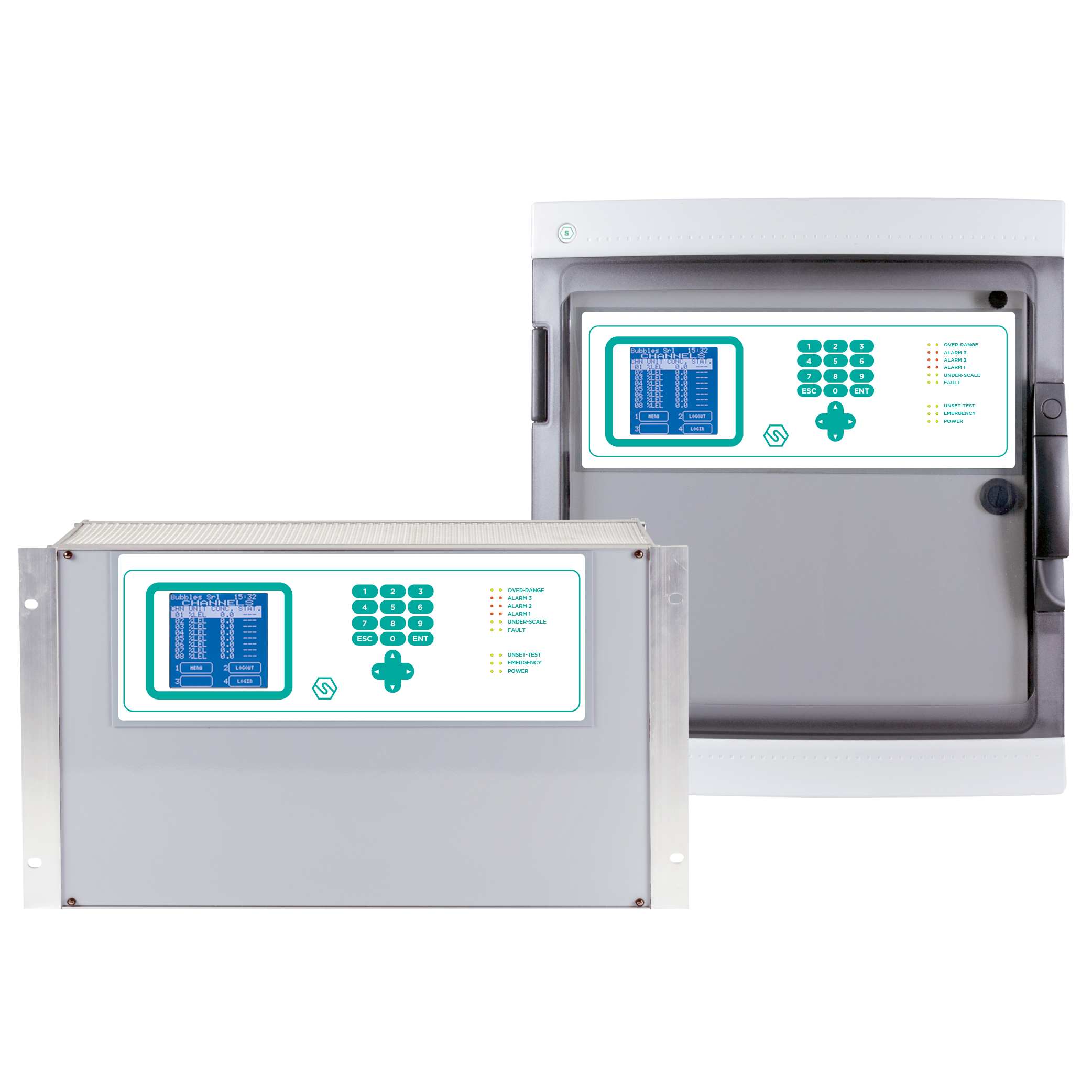
MULTISCAN++ S1/S2
Designed to meet the widest market demand for flexibility, they allow the management of up to 264 detectors. ATEX and SIL certified.
Our certifications
In hazardous environments where strict safety standards must be met, it is important to use products that are certified and in line with regulations. Discover our certifications:
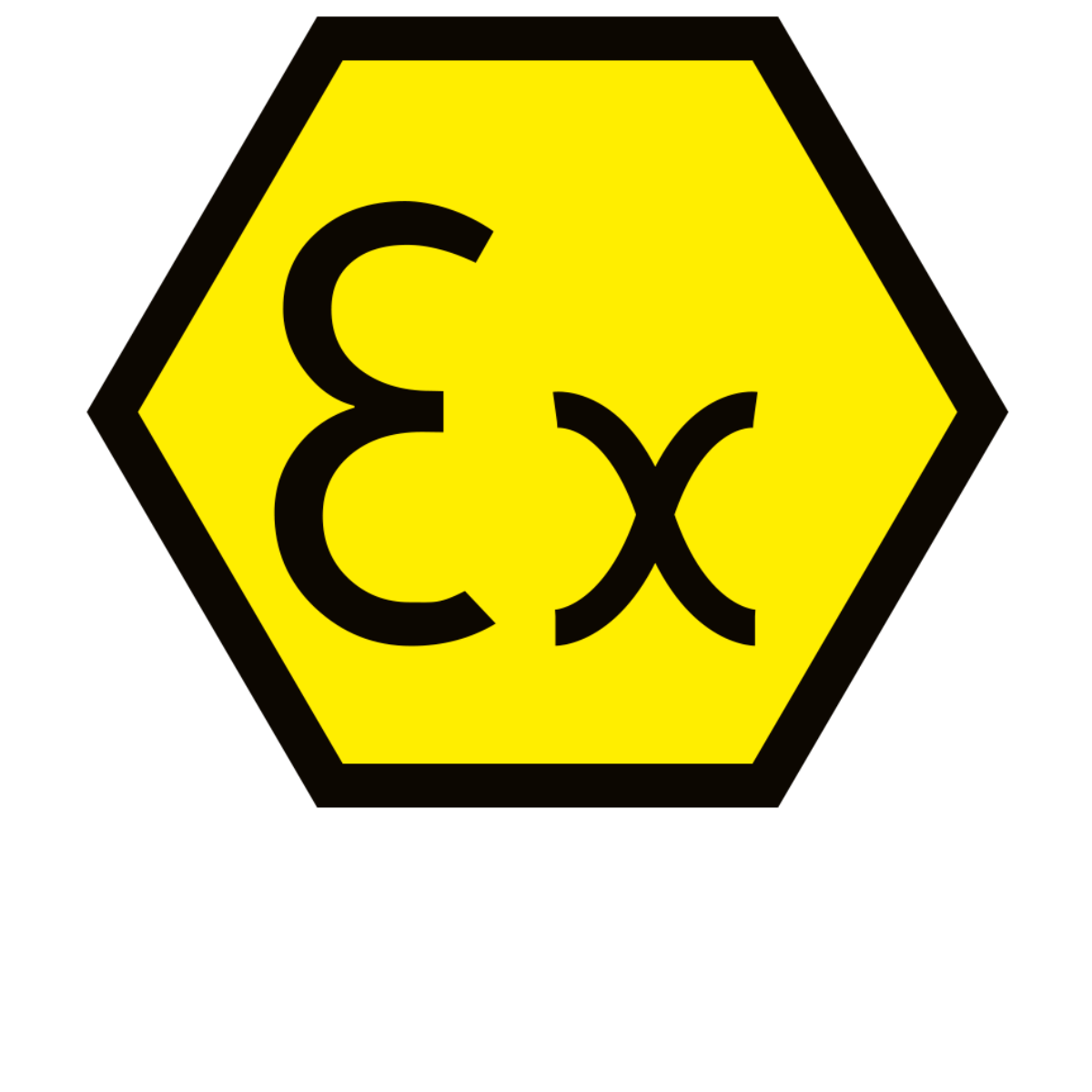
ATEX
The Directive sets out the requirements and assessment of equipment intended for use in potentially explosive atmospheres.
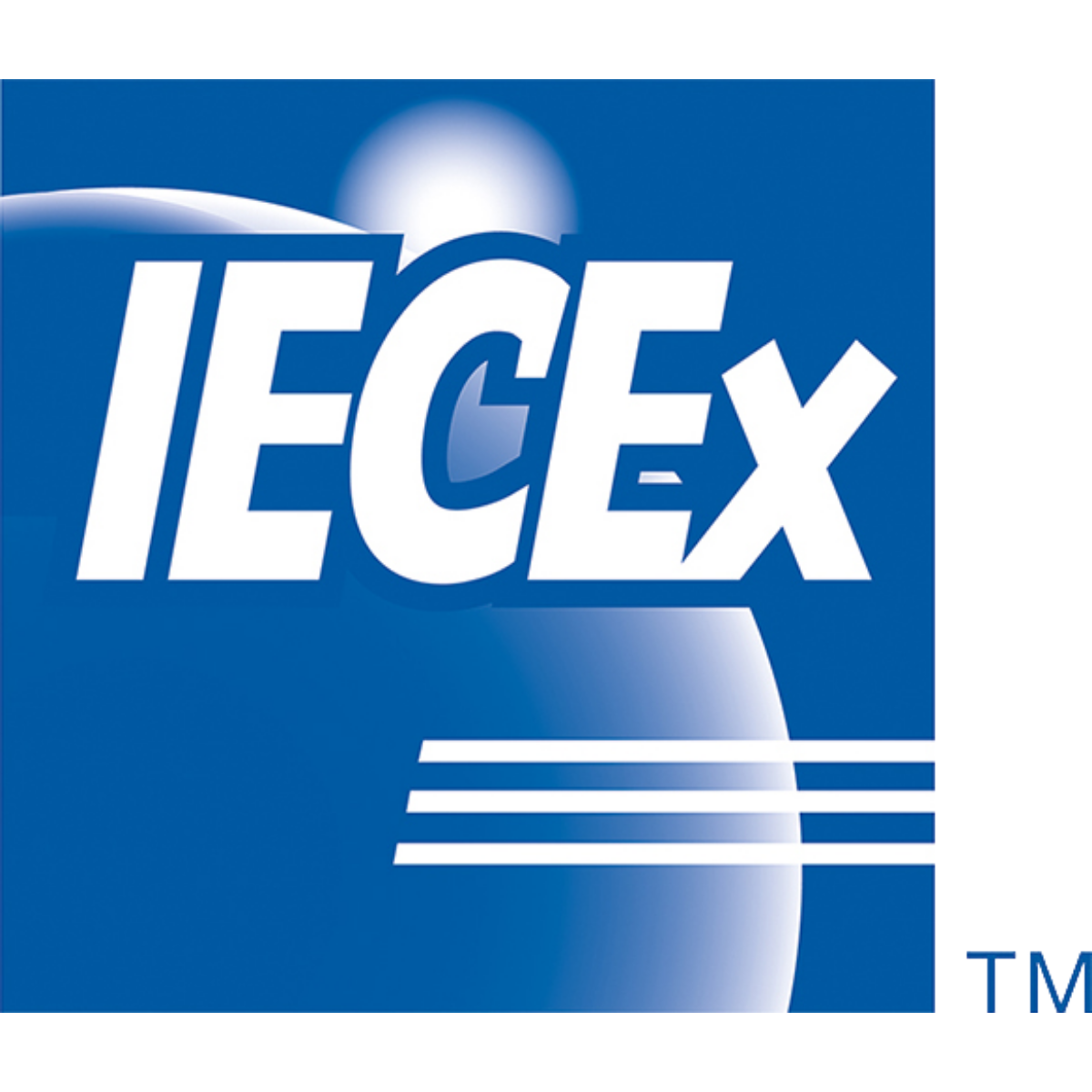
IECEx
The IECEx system is an international certification system. It is developed by the International Electrotechnical Commission.
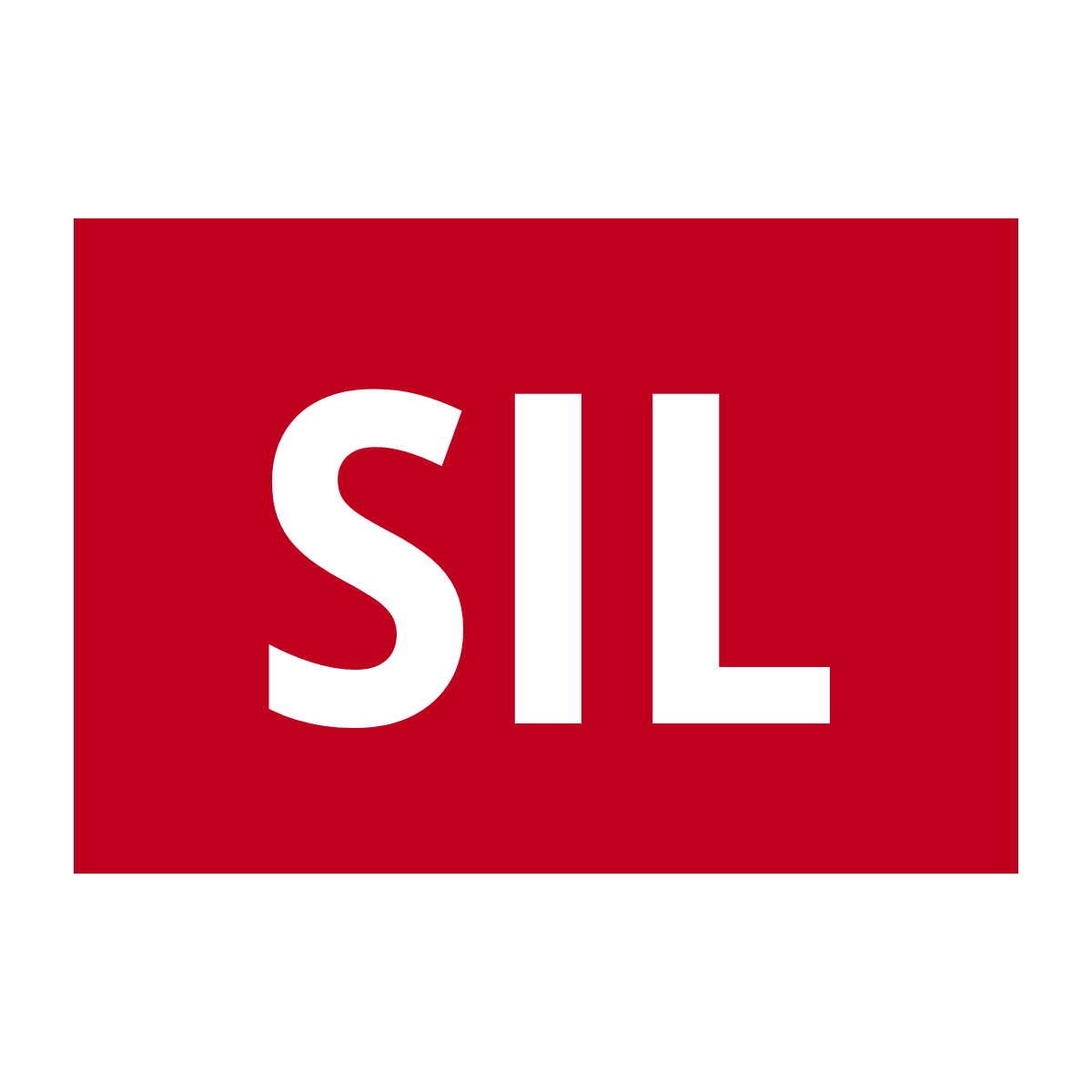
SIL
The Safety Integrity Level (SIL) is the ability to reduce the assessed risk by ensuring the reliability of safety systems.