In the chemical industry, gas management and control are key aspects in ensuring the safety of operators, plants and the environment. Gas detection is not only a mandatory practice from a regulatory point of view, but also a strategic element to prevent accidents and optimize production processes.
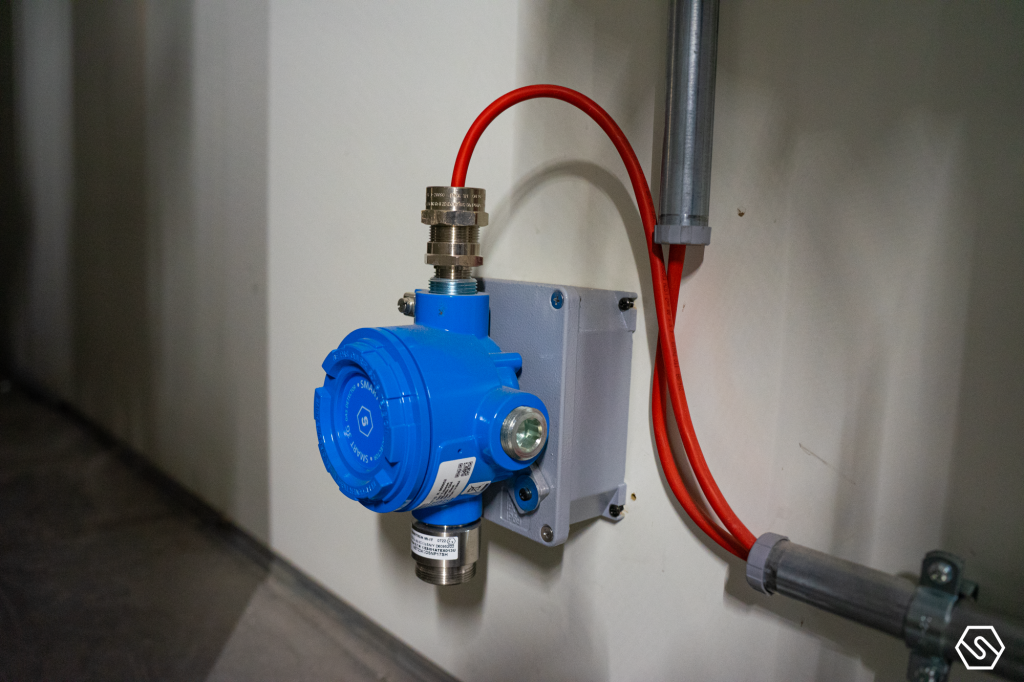
Chemical industry and gas detection: what are the crucial aspects
Chemical companies work with a wide range of potentially hazardous substances, such as toxic and flammable gases. Uncontrolled release of these substances can have devastating consequences, including:
- Health hazards: Acute or chronic exposures to toxic gases can cause serious health problems for operators.
- Industrial accidents: The presence of flammable gases increases the risk of explosions and fires.
- Environmental impact: Leakage of harmful gases can damage the surrounding ecosystem.
- Early detection of these gases allows for risk mitigation, protecting not only people but also plants and land. It also helps comply with environmental regulations and maintain high operational standards
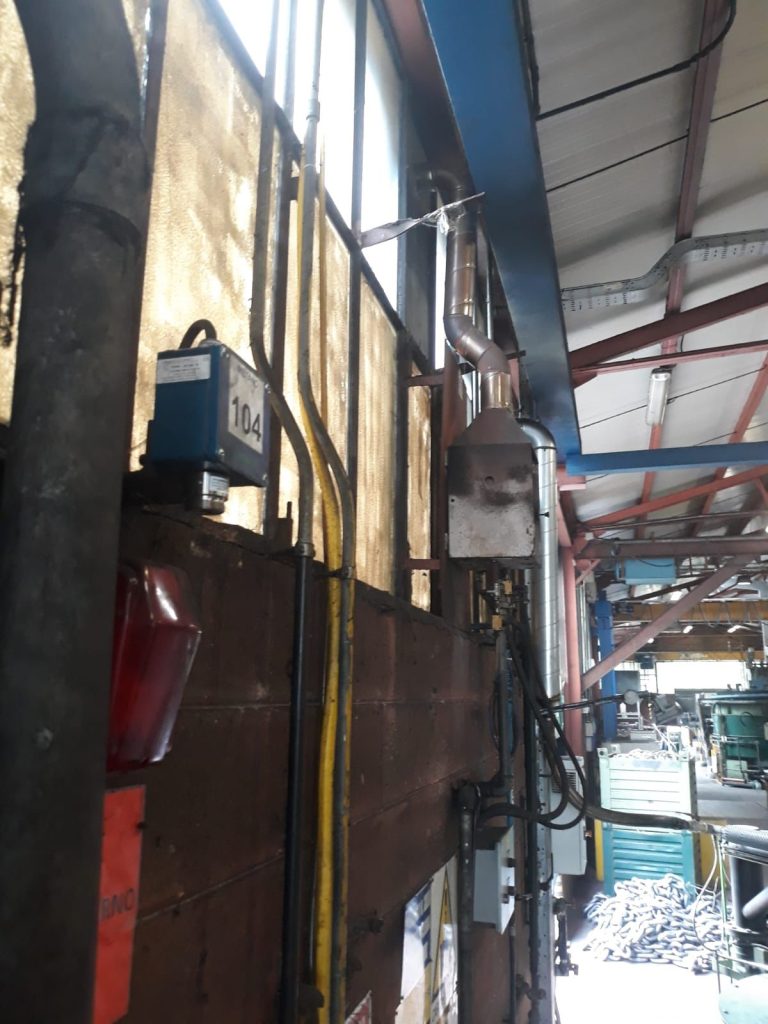
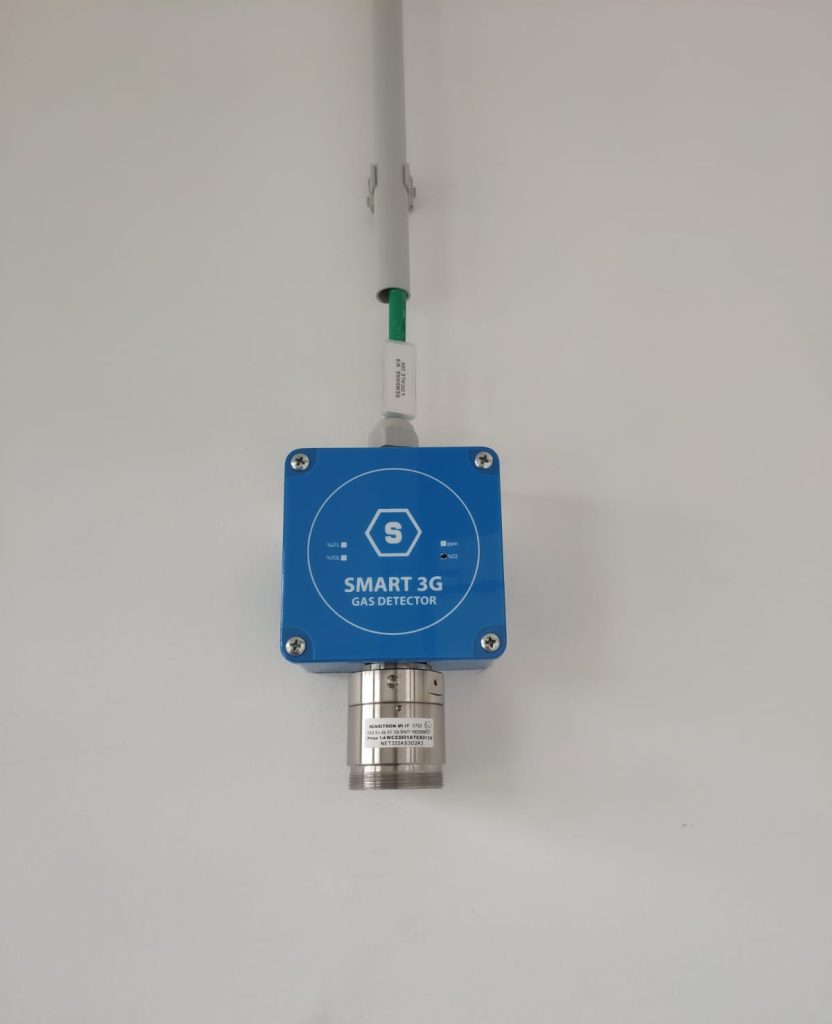
Gas detection in the chemical industry: what are the most common gases
In the chemical industry, some gases are particularly relevant because of their impact on safety. Some of the most common include:
- Methane (CH4): Flammable gas used as a fuel; its dispersion can lead to explosion hazards.
- Ammonia (NH3): Used in many industrial processes, it is toxic and corrosive.
- Chlorine (Cl2): Essential in several chemical sectors, but highly toxic even at low concentrations.
- Carbon Monoxide (CO): A colorless and odorless gas, it is extremely dangerous to human health.
- Carbon Dioxide (CO2): Although non-toxic in small concentrations, it can cause asphyxiation in confined environments.
- Hydrogen Sulfide (H2S): A toxic gas with a characteristic smell of rotten eggs, it is dangerous even at relatively low concentrations.
Knowledge of the most common gases and their characteristics is essential for choosing the most appropriate detection technologies. Conscious management of hazardous substances can significantly reduce risks and ensure greater operational efficiency.
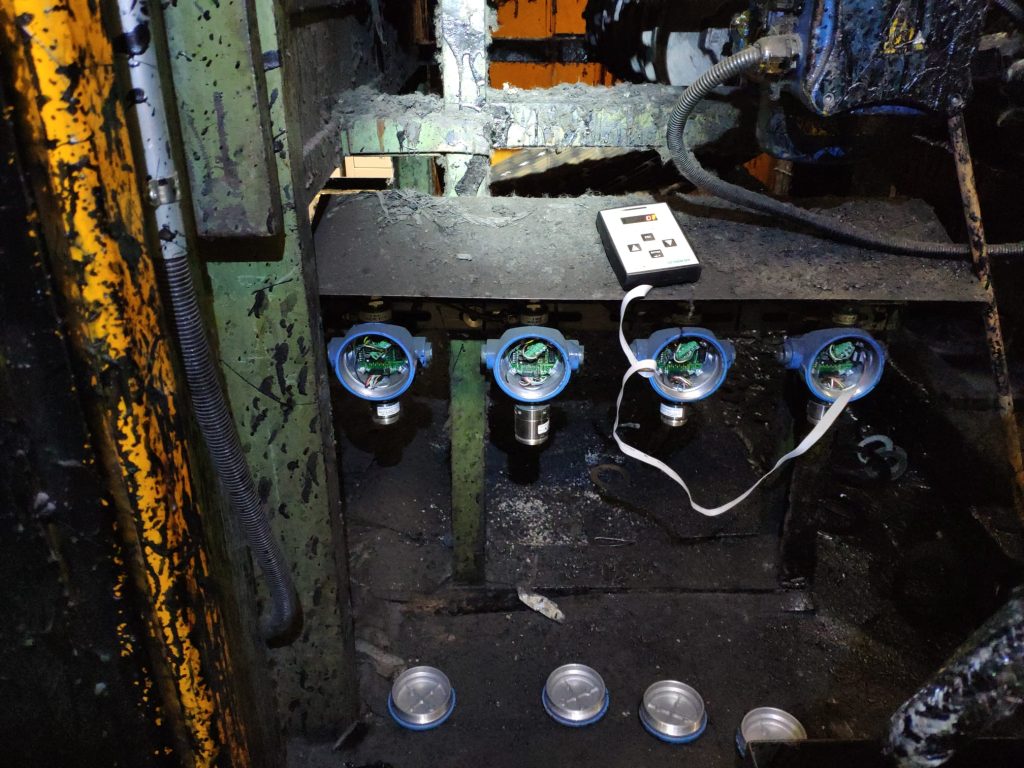
Gas detection in the chemical industry: what technologies are used
Thanks to technological advances, it is now possible to monitor the presence of gases with highly advanced instruments designed to operate in complex industrial environments. Among the main technologies used are:
- Infrared detectors: Ideal for gases such as methane and carbon dioxide, offering accuracy and resistance to environmental interference.
- Electrochemical sensors: Used for toxic gases such as carbon monoxide and chlorine, they provide fast and accurate responses.
- Photoionization detectors (PIDs): Suitable for detecting volatile organic compounds (VOCs), they offer high sensitivity and accuracy.
- Catalytic detectors: Used for flammable gases, they are robust and reliable, although they require regular maintenance.
Discover our produtcs
Sensitron gas detectors are suitable for use in any application:
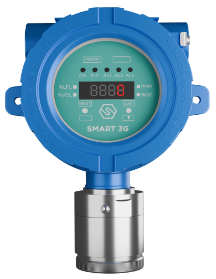
SMART 3G D2
Suitable for detecting the presence of flammable substances, toxic gases, refrigerants and oxygen in classified areas.ATEX, IECEx and SIL2/3 certified
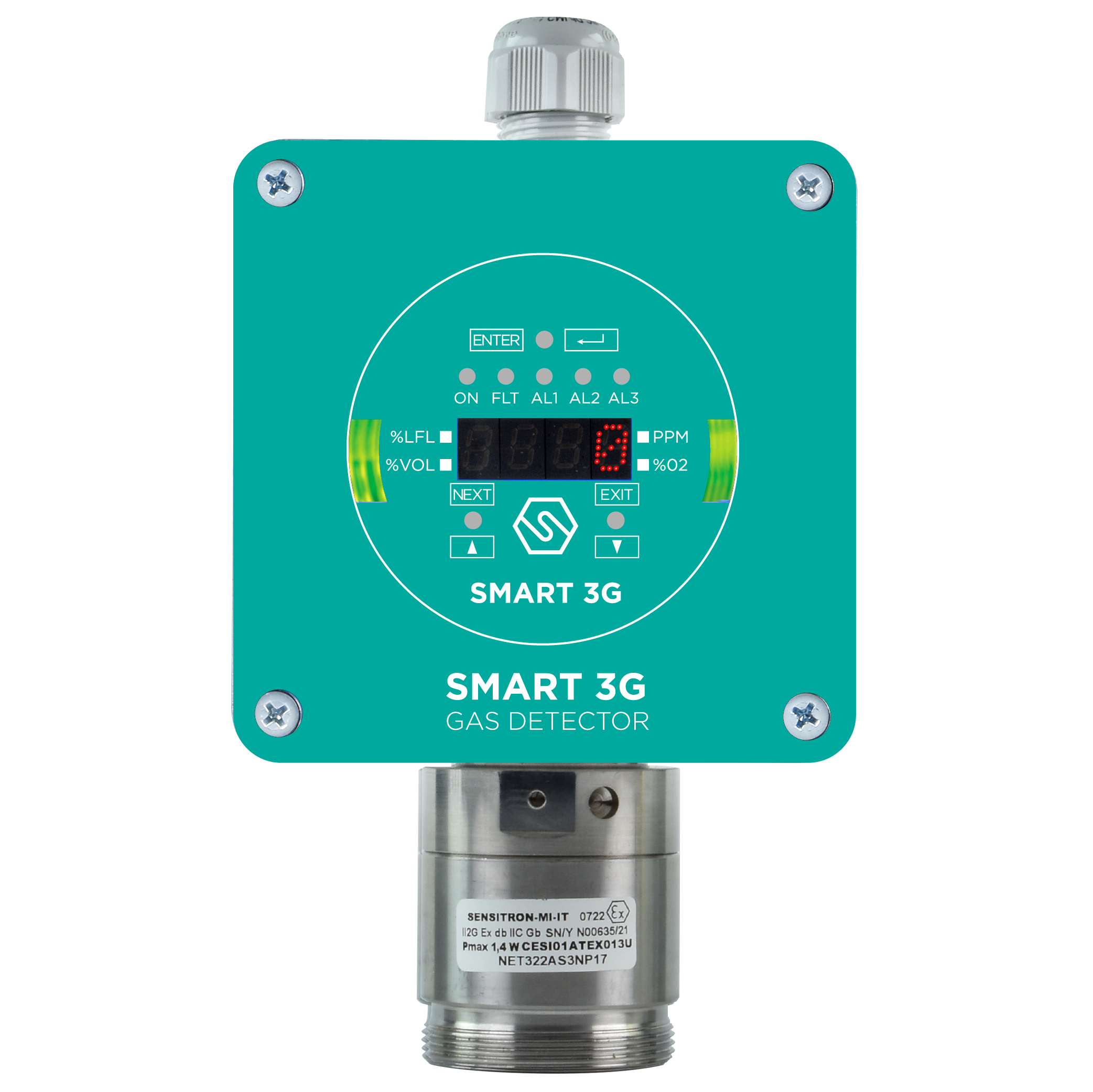
SMART 3G D3
Suitable for detecting in classified areas,ATEX, IECEx and SIL2/3 certified, enables non-intrusive field calibration.
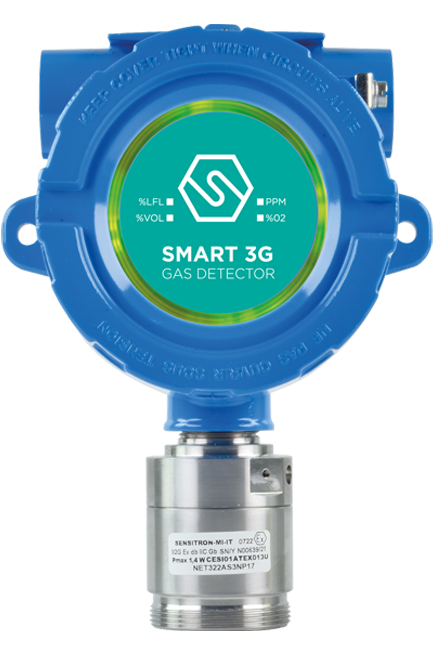
SMART 3G C2
Suitable for detecting, in classified areas, the presence of flammable substances (% LFL), toxic gases in ppm, refrigerant gases or for the detection of oxygen deficiency or excess.
Our certifications
Within hazardous environments where strict safety standards must be met, it is important to use products that are certified and in line with regulations. Learn about our certifications:
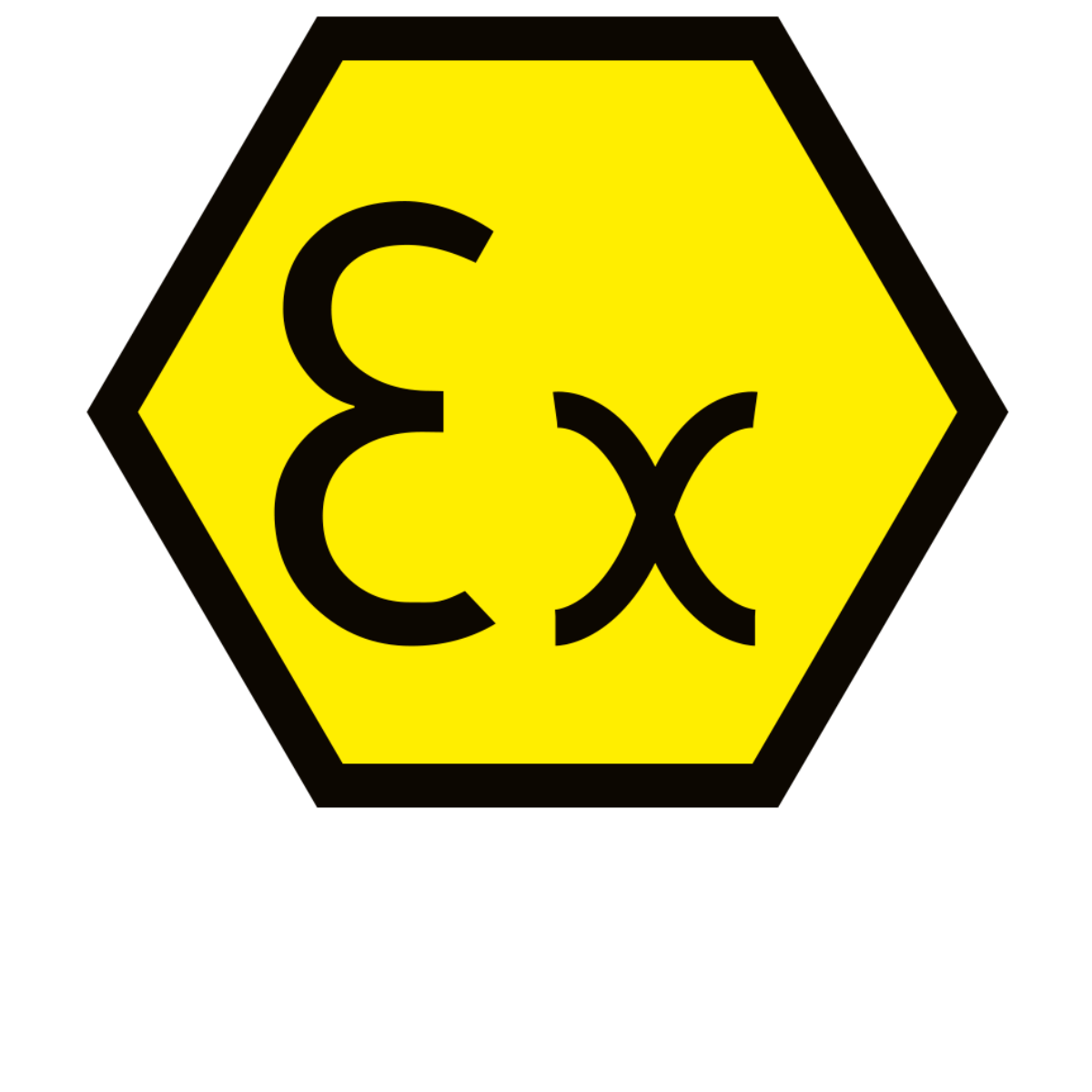
ATEX
The Directive sets out the requirements and assessment of equipment intended for use in potentially explosive atmospheres.
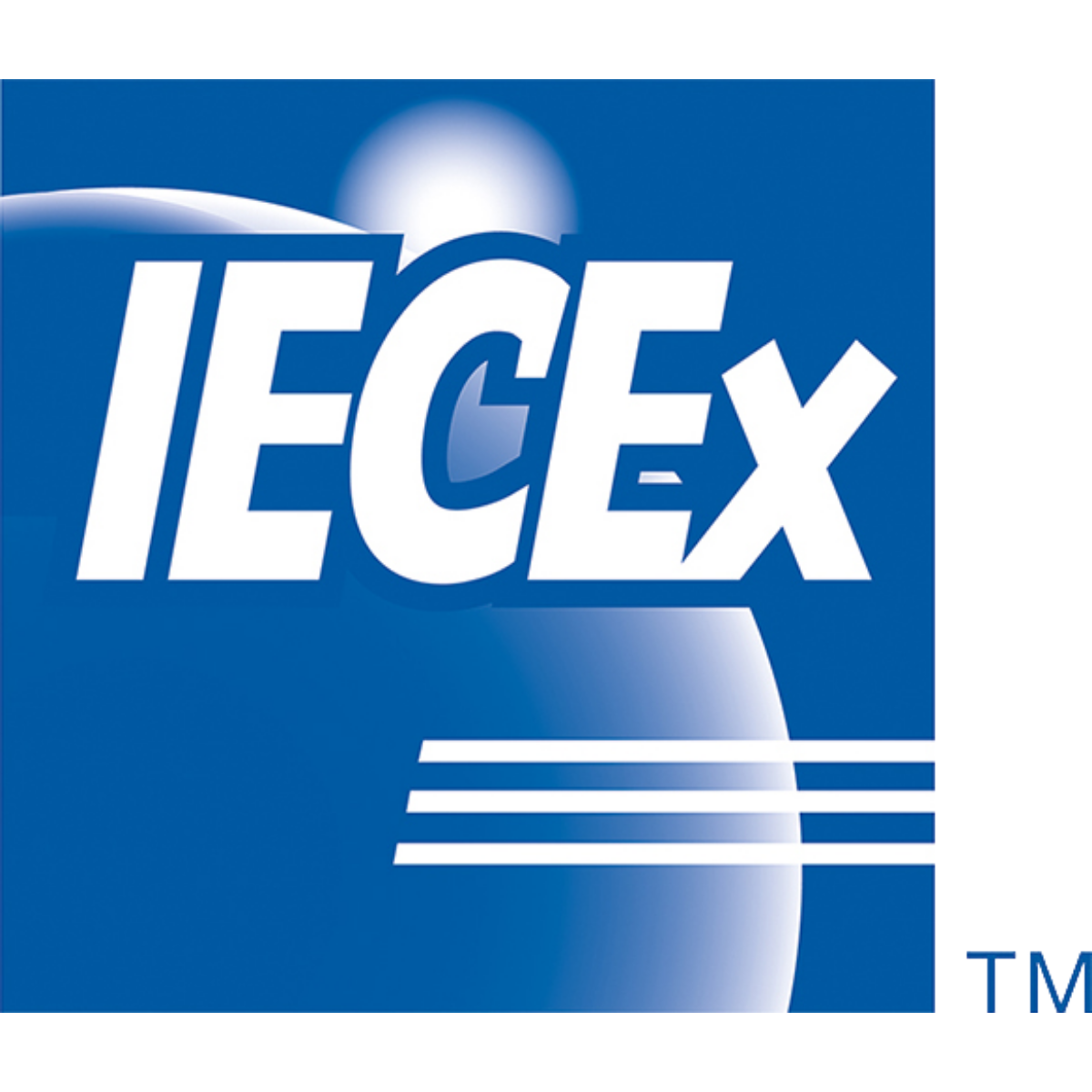
IECEx
The IECEx system is an international certification system. It is developed by the International Electrotechnical Commission.
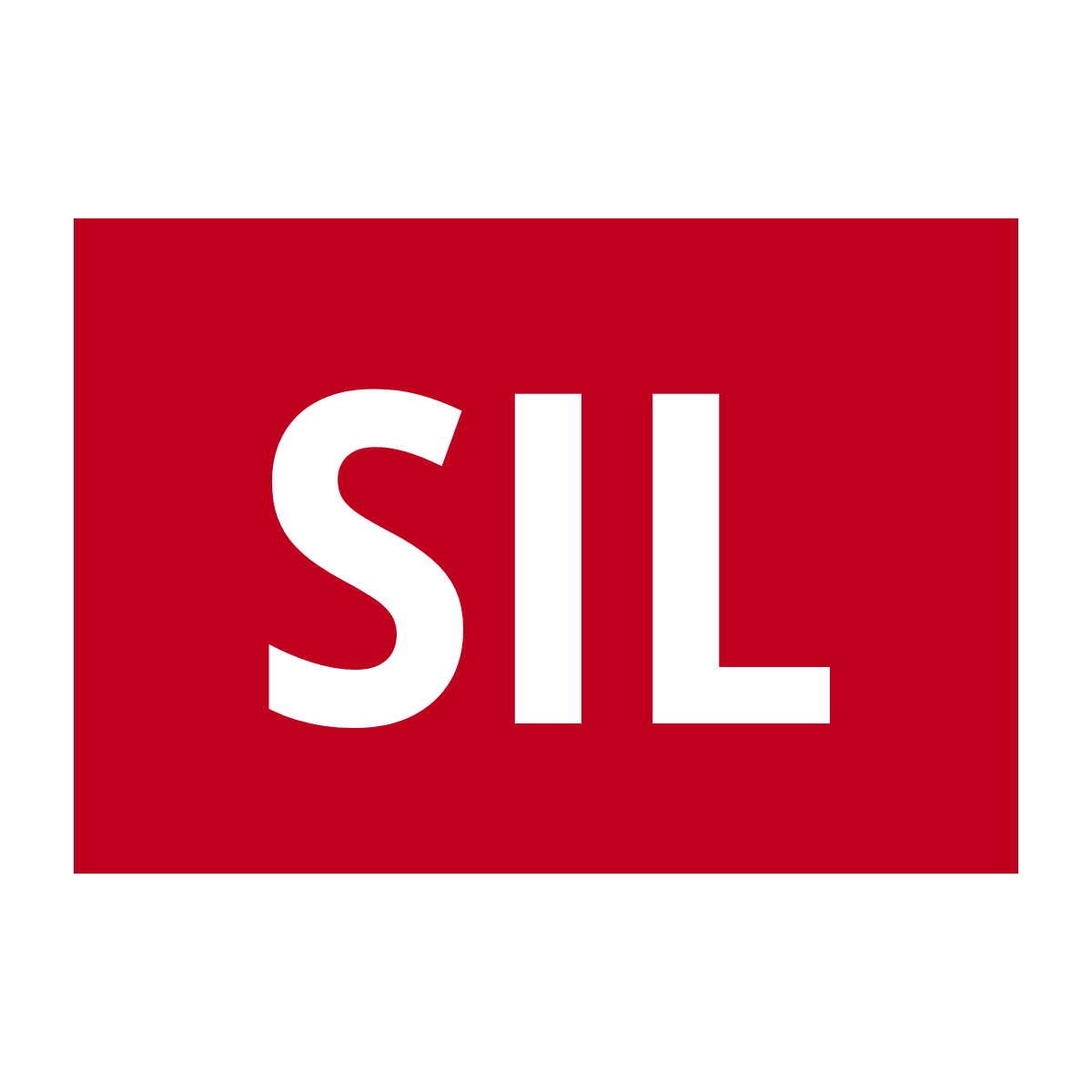
SIL
The Safety Integrity Level (SIL) is the ability to reduce the assessed risk by ensuring the reliability of safety systems.