Gas detection in engine rooms is a crucial element in ensuring the safety of people, environments, and equipment. These spaces, often used to house technological equipment such as compressors, generators, and HVAC systems, are characterized by a high concentration of sensitive equipment and, in some cases, a significant risk of hazardous gas accumulation.

Machine rooms: the advantages of gas detection
Machine rooms may contain combustible, toxic or asphyxiating gases that, if not detected in a timely manner, can cause:
- Explosions or fires: caused by the presence of combustible gases in hazardous concentrations.
- Health hazards: due to exposure to toxic gases such as carbon monoxide or ammonia.
- Equipment damage: corrosion and equipment malfunction can be indirect consequences of the presence of harmful gases.
Engine rooms represent complex environments that pose several challenges for gas detection. Tight spaces, for example, can restrict air movement and encourage gas accumulation in specific areas. In addition, operating conditions are often variable, with temperatures and humidity levels that can affect the effectiveness of detection systems. Finally, the presence of a wide range of gases requires versatile and customized solutions to ensure complete and reliable coverage.
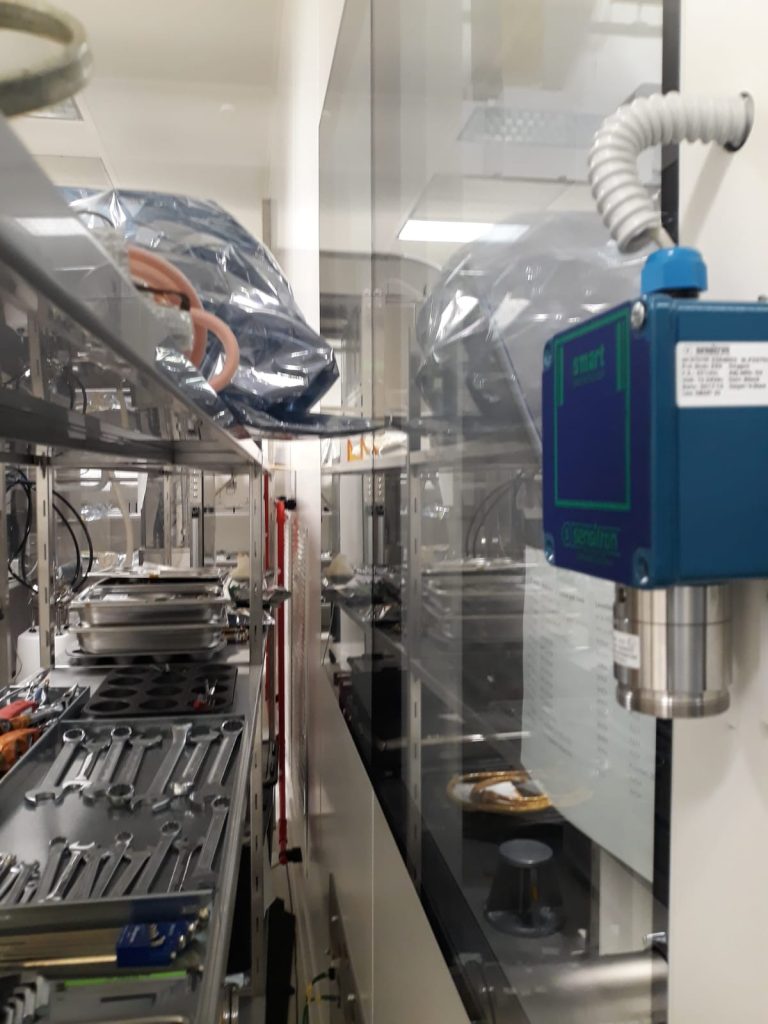
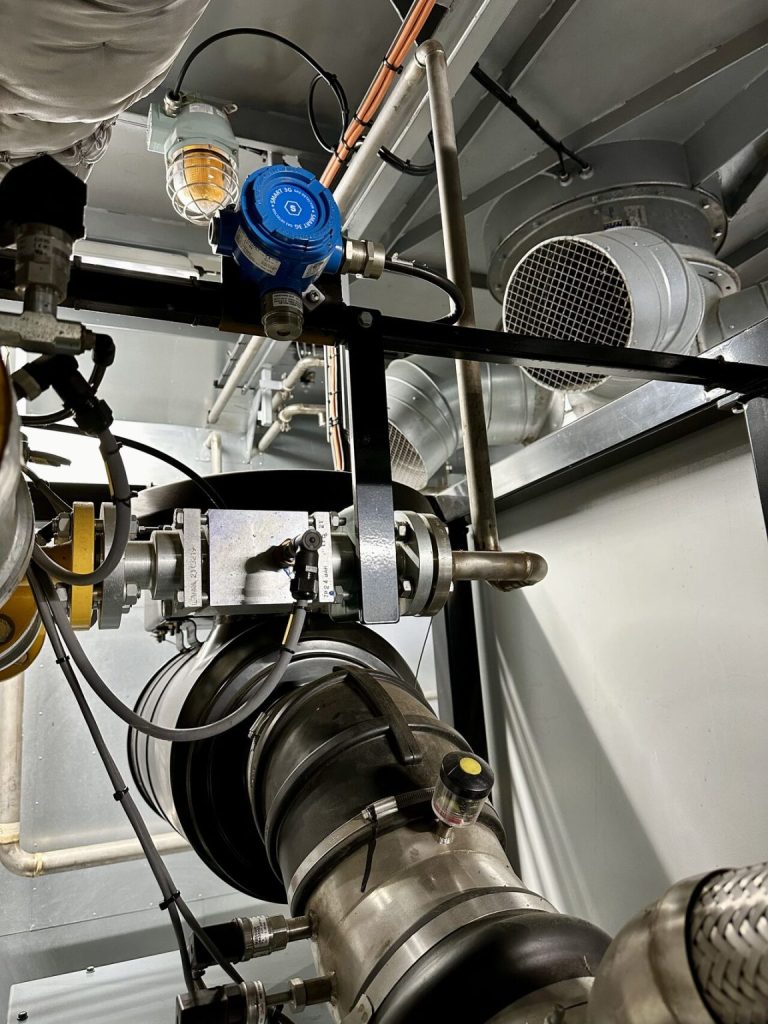
Technologies for gas detection in engine rooms
To meet these challenges, gas detection systems employ a variety of technologies:
- Catalytic sensors: ideal for combustible gases, they work by oxidizing the gas in the presence of oxygen and generating a proportional electrical signal.
- Infrared (IR) sensors: used for specific gases such as carbon dioxide, methane or refrigerant gases, they offer reliability even in humid environments.
- Electrochemical sensors: suitable for toxic gas detection, they are extremely accurate and sensitive.
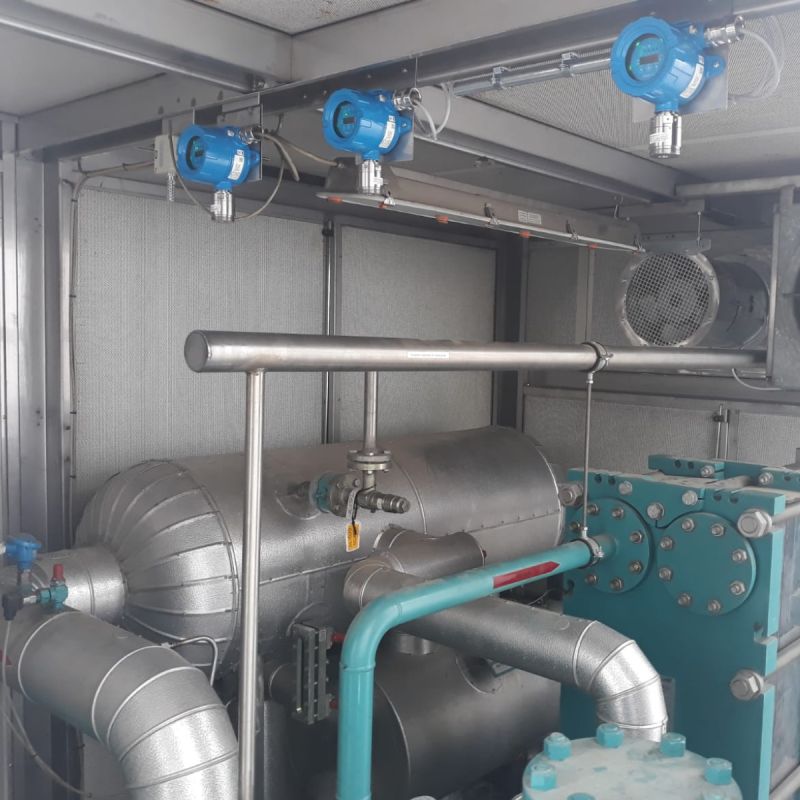
Machine rooms: the most common applications
Gas detection in machine rooms finds application in a wide range of industrial and technological settings. Some of the most common applications include:
- Refrigeration plants: for monitoring refrigerant gases such as ammonia or fluorinated gases.
- Power plants: where the presence of combustible gases such as methane requires continuous monitoring to prevent explosion hazards.
- Chemical industry: for monitoring toxic or corrosive gases in production processes.
- Data centers: where it is critical to detect leaks of gases used in fire protection or air conditioning systems.
Discover our produtcs
Sensitron gas detectors are suitable for use in any application:
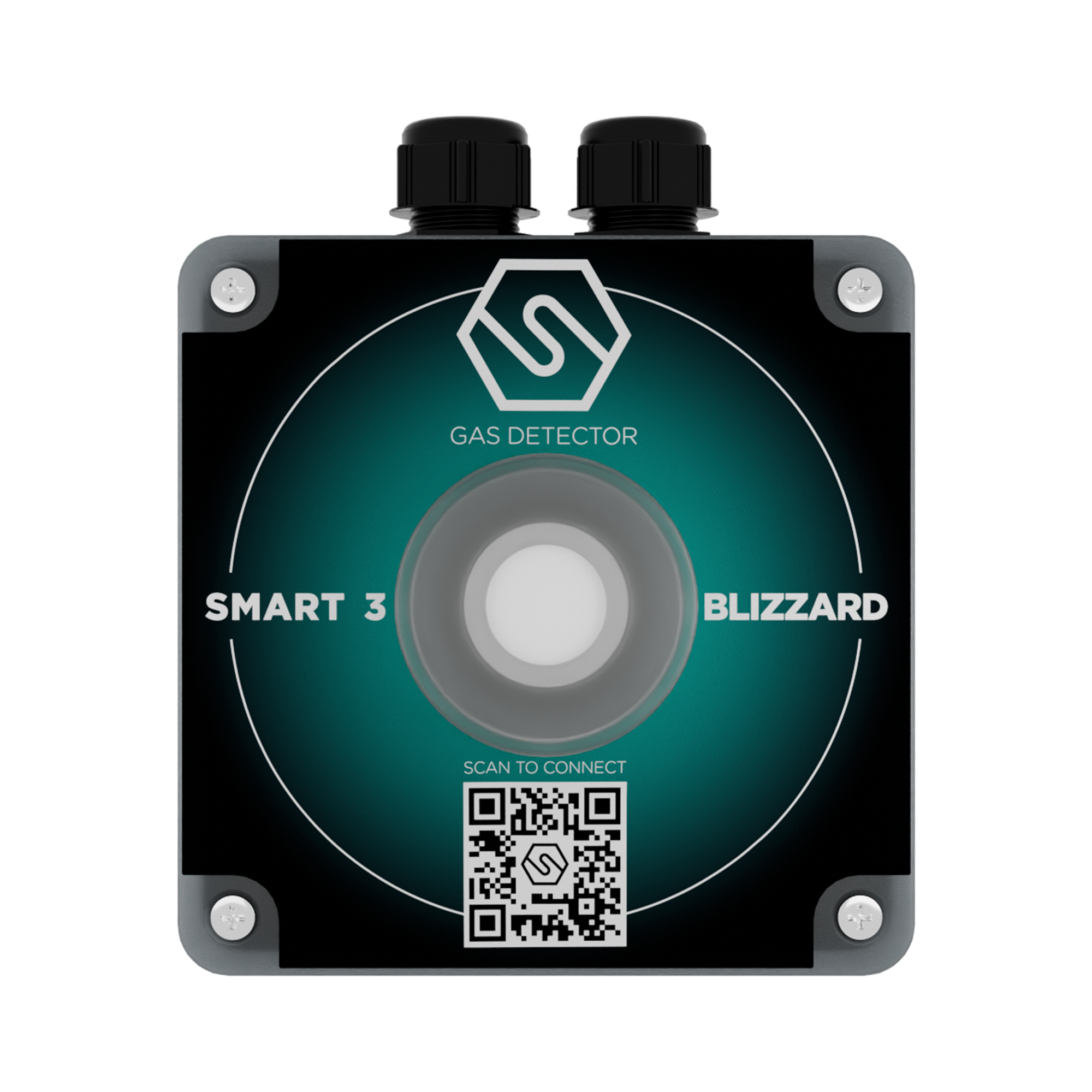
SMART 3 BLIZZARD
Suitable for detecting the presence of A1 and A2l refrigerant gases in unclassified areas, thanks to its SENSE interface it can be remotely controlled.SIL2 certified, complies with F-gas regulation
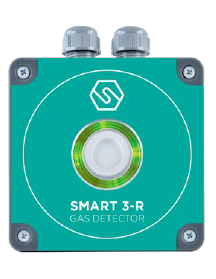
SMART 3 R
The SMART3 R detector enables the detection of explosive, toxic and refrigerant gases in unclassified areas, ideal for machine rooms and light industry. Meets F-gas regulation
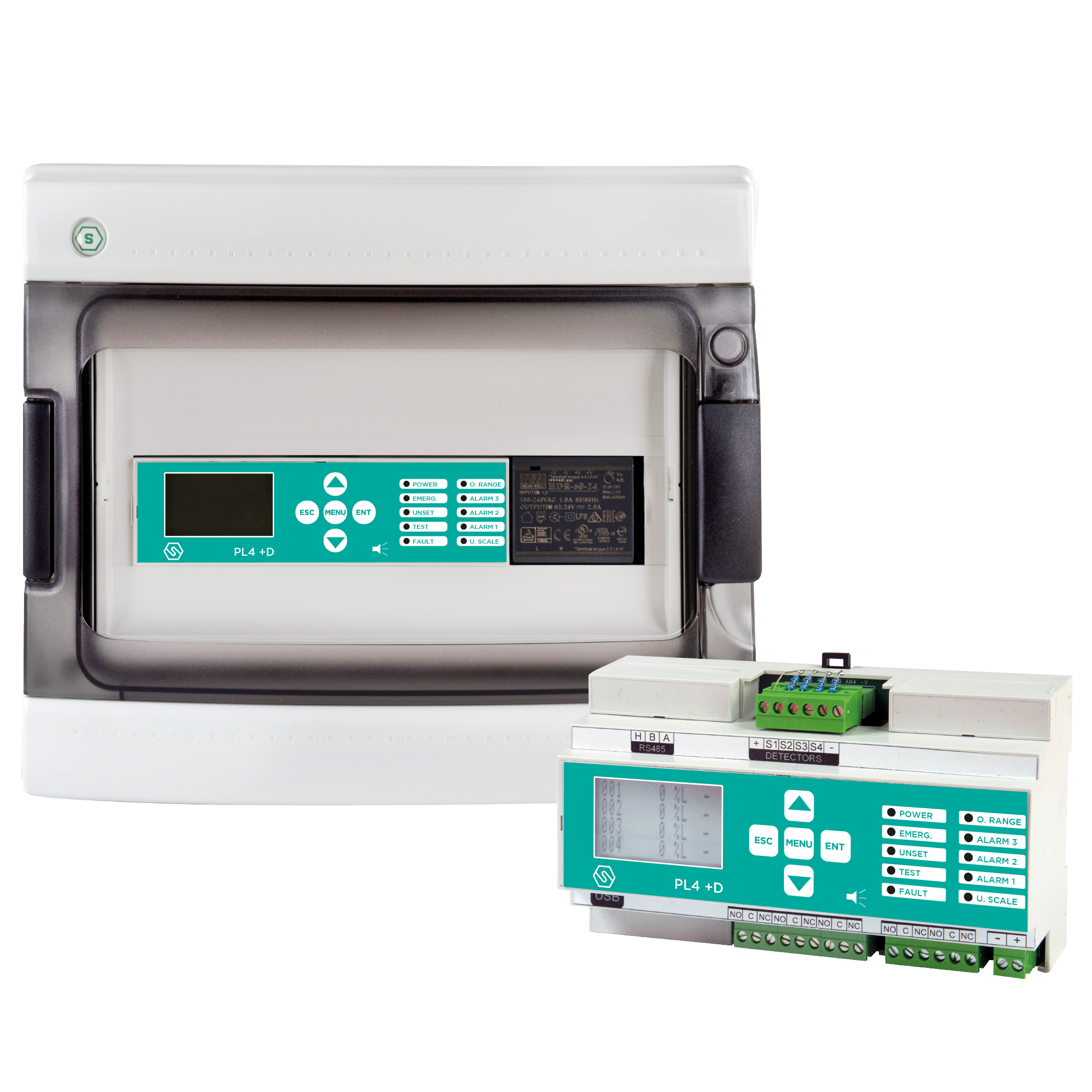
PL4+
The PL4+ gas detection panel represents the best technology for flammable, toxic and oxygen gas detection in small systems
Our certifications
Within hazardous environments where strict safety standards must be met, it is important to use products that are certified and in line with regulations. Learn about our certifications:
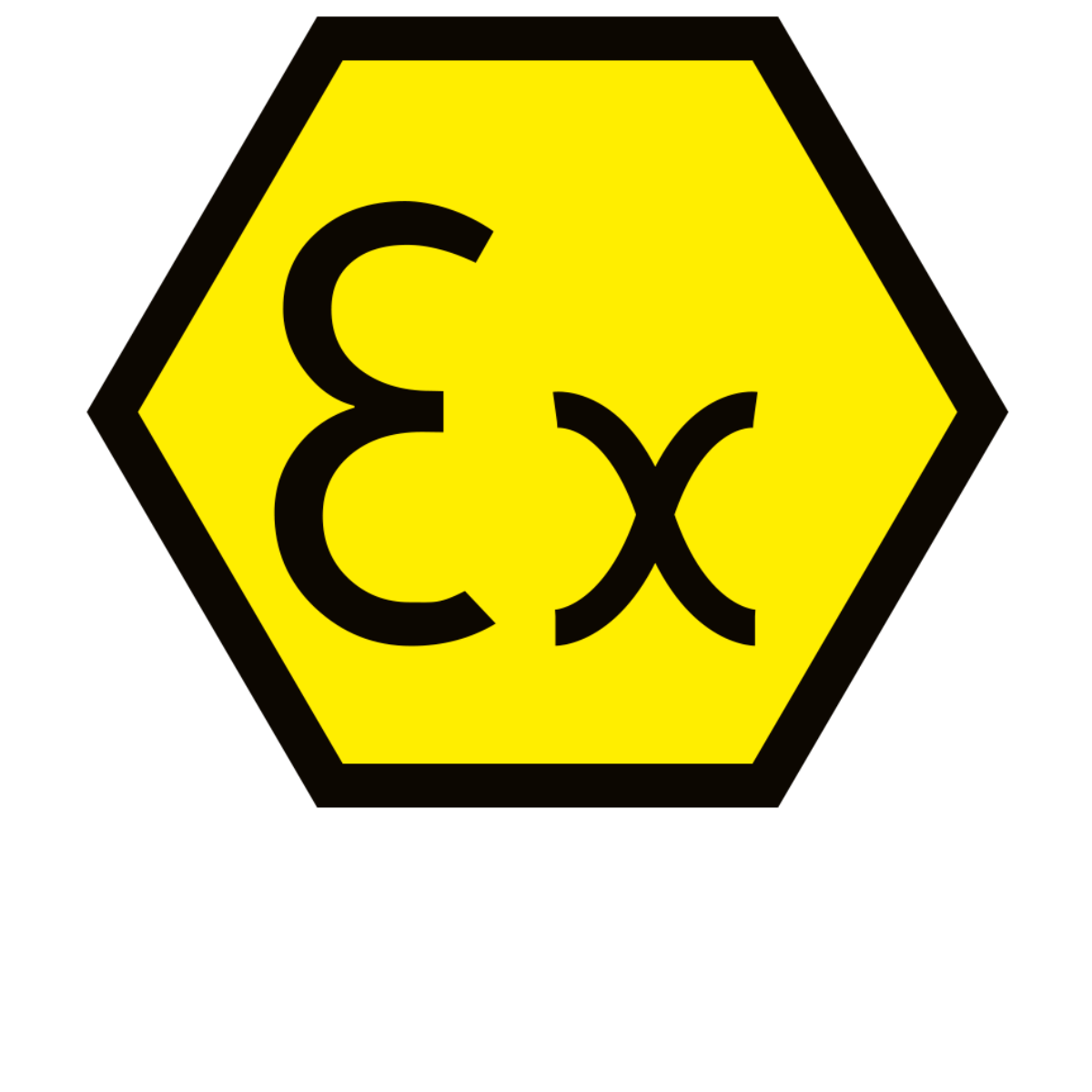
ATEX
The Directive sets out the requirements and assessment of equipment intended for use in potentially explosive atmospheres.
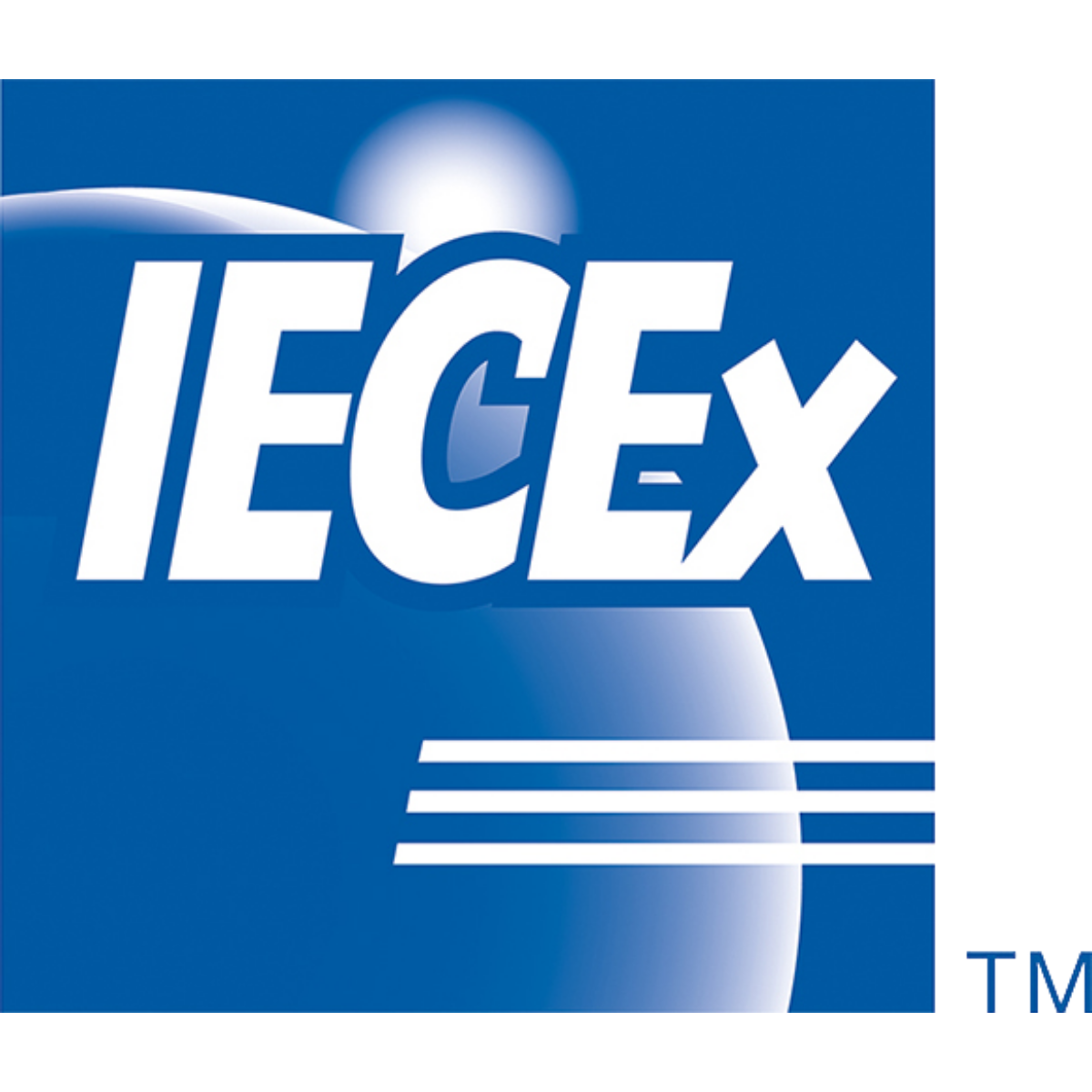
IECEx
The IECEx system is an international certification system. It is developed by the International Electrotechnical Commission.
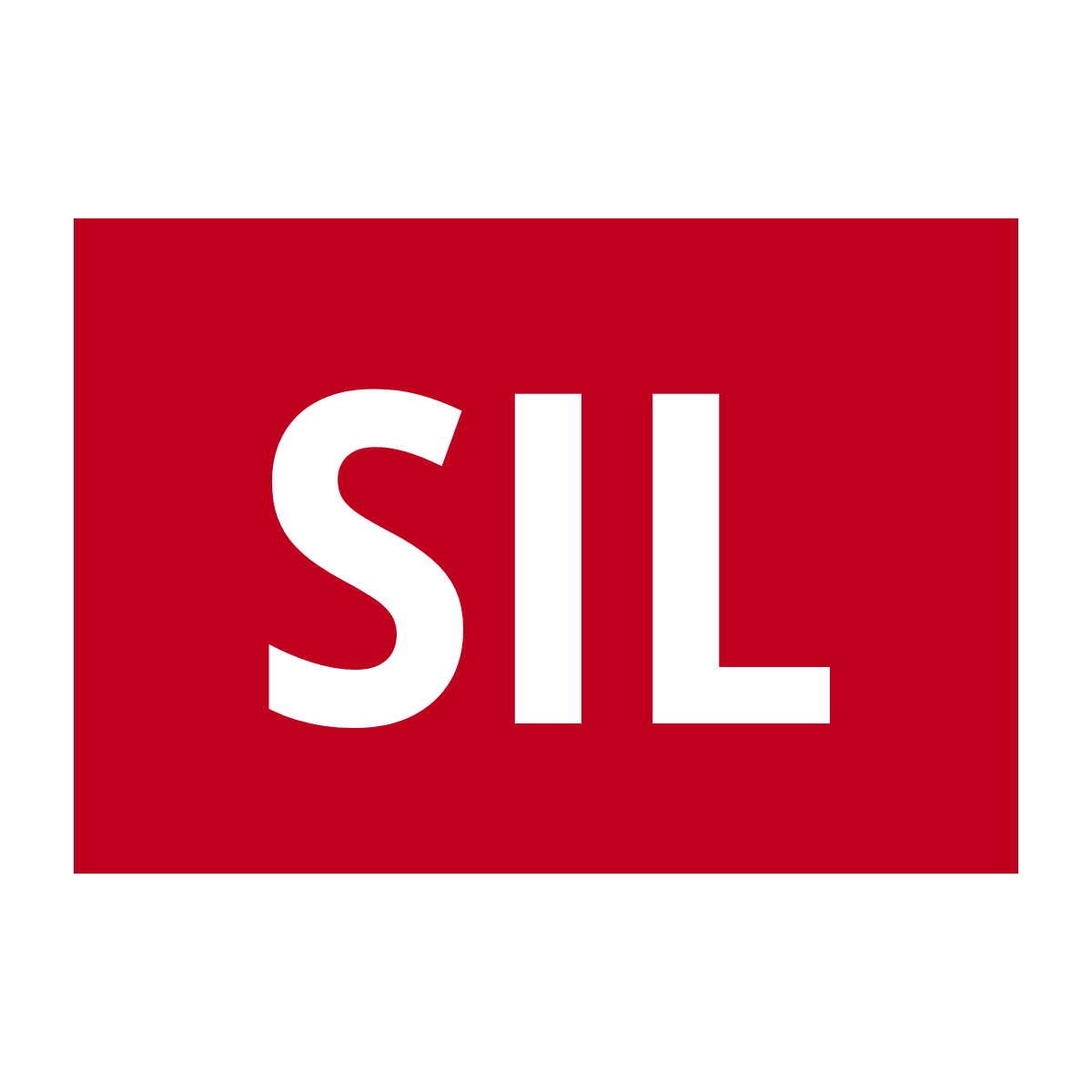
SIL
The Safety Integrity Level (SIL) is the ability to reduce the assessed risk by ensuring the reliability of safety systems.